摘要:钻井废水、钻井柴油机废气污染物和排气噪声是石油天然气钻探作业环境保护的主要治理对象。根据热力学原理和气液动量、热量、质量传递相变机理,研发了钻井废水废气同步消减新技术。其技术原理为:钻井废水与柴油机废气两相流直接接触传热传质,废气余热消减废水,废水吸收废气烟尘同时使废气降温降噪减阻,替代柴油机排气消声器。为此,设计了与钻井190型涡轮增压柴油机配套的ST系列废水废气现场同步处理示范装置,并在四川龙岗和新疆克拉玛依等多种地质结构的油气钻井现场实施。结果表明,单台810kW柴油机1200r/min工况下平均消减废水能力为0.538m3/h,废气烟尘基本消除,降噪效果比消声器提高4.2%~23.7%(倍频带)而背压降低70%以上,柴油机功率损失比减少1%。实践证明,该技术改变了钻井废水末端治理的现状,以源头治理方式实现钻井现场废水不加药、不外排、不转运,为提高钻探作业环保水平提供了可靠的技术保障,对建立石油天然气钻探清洁生产体系具有重要意义,并可以大幅度减少钻井现场废水池征地和基建投资,产生显著的经济、环境和社会效益。
关键词:钻井废水;柴油机废气;同步处理;源头治理;环境保护;节能减排
0 引言
世界各国对石油天然气钻采环保采取越来越严格的措施,欧洲北海油气田、科威特大布尔甘油田和美国马塞勒斯页岩气田等不同国家与类型油气钻采废水管理均倾向于零排放和循环利用,规避环境风险[1~3]。我国钻井废水处理技术近10年来有很大进展,但仍以末端治理、达标排放为主[4~6]。为适应我国日益严格的环保法规和公众的环保要求,石油行业“十一五”规划提出了增产不增污,建立环境友好石油天然气钻采清洁生产体系的任务[7]。
四川大学承担国家“863”计划课题对钻井废水源头治理技术进行系统研究,与广汉欣欣实业有限公司共同开发了钻井废水废气同步消减新技术及成套橇装设备[8]。本文基于在四川龙岗和新疆克拉玛依等多种地质结构的油气钻井现场示范应用中积累的原始资料,介绍该技术的原理、设计要点、现场实施效果及其产生的环境与经济效益。
1 技术原理与设计要点
1.1 废水废气同步消减原理与流程
根据气液两相流直接接触传热传质等焓过程原理[9],设柴油机排气温度(t)、湿含量(H)、比热(Cp),与废水传热传质达到饱和温度(ts)、饱和湿含量(Hs),废水汽化热(γ),则单位质量废气饱和增湿量理论值为:

按上式绘制的t-△w和t-ts曲线见图1。
由t-△w曲线可见,废气饱和增湿量与柴油机排气温度呈线性关系,在240~450℃的排气温区△w变化范围为0.084~0.175(kg/kg废气),增长约1倍。190型涡轮增压柴油机额定工况(810kW)排气量Q=5275kg/h,排气温度t=330℃,对应△w=0.123(kg/kg废气),则排气消减废水量理论值为:
Wmax=△w×Q=0.123×5275≈649(kg/h) (2)
对应的废热回收与柴油机输出轴功率之比为:

图1的t-ts曲线还提供了与柴油机排气温度(t)相对应的饱和温度(ts),若实测同步处理后废气温度下降到tout,则根据式(3)定义的设备运行效率可判断运行状态,一般应在90%~98%范围。

本技术原理流程如图2所示。废水池来的原水与柴油机废气逆流进入设备,气-液两相交叉流传热传质,废水蒸发浓缩,废气降温增湿且所含烟尘等有害物质被废水吸收排往沉积池。
1.2 降噪与减阻设计要点
上述过程同步产生排气降噪减阻功能,可替代消声器并减少柴油机功率损失。研究显示[10],额定工况下190型涡轮增压柴油机排气消声器阻力损失为2.3~2.5kPa,其功率损失比为1.6%~4.0%。本技术利用废水废气同步消减装置气-液传热传质表面吸波、气体体积收缩和流道结构自振频率低等效应,可有效降低排气噪声(尤其是高频)。这种内源式降噪机理可使消声阻力降至原有消声器的1/3~1/4,即小于或等于0.8kPa,柴油机功率损失比减小至少1%。设计依据流体阻力计算公式[8]:

通过结构优化,获得保证△p≤0.8kPa的参数如下:
阻力系数λ为0.02~0.03;
废气表观流速u≤12m/s;
装置附属直管长度L≤20m;
装置内部阻力当量长度∑Le≤40m;
装置流道当量直径de≥0.3m。
其中,∑Le是气-液两相交叉流流道局部阻力的总和,当量直径de按非圆型截面流道定义:

按此设计的ST系列钻井废水废气同步处理装置,柴油机配带后现场实测排气背压均低于0.8kPa。
2 现场示范运行效果
图3是ST-A型装置(单机配带)在LG17井现场对比试验运行实况,图4是ST-C型装置(三机配带)在合川001-6-X3井现场安装实况,均随钻井全周期同步运行,取得了废水源头治理和废气消烟、降温降噪的良好效果。
2.1 废水消减量
2008年6月LG17井3#柴油机配带ST-A型废水废气同步消减装置(图3)替代排气消声器,与2#机对比进行验证试验。钻井队按惯例轮换使用3台柴油机,划眼、钻进、起下钻及启动、停车等不同阶段全程运行验证了实验机运行平稳。记录(表1)显示,3#机累计运行46.2h(划眼7h、钻进39.2h),ST-A型装置消减废水累计量23.9m3,平均消减能力为0.517m3/h。钻进阶段柴油机转速1200r/min,平均消减废水0.538m3/h;划眼阶段柴油机转速900r/min,平均消减废水0.40m3/h。
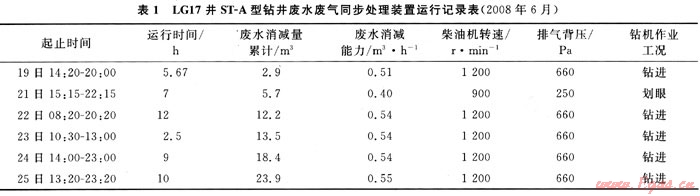
2009年10~11月合川001-6-X3井(井深2476m)3台钻井柴油机配带ST-C型废水废气同步消减装置,钻井全程井场产生废水量201m3,本技术消减废水量187m3,废水池仅剩余14m3。
2.2 减阻与降噪效果
LG17井38机配带ST-A型废水废气同步消减装置与2#机对比,排气背压(表1)与噪声(表2)同步下降。钻进工况为柴油机转速1200r/min,2#机排气背压实测值2.3~2.5kPa,3#机仅660Pa,降低70%以上。该工况下按噪声监测规范在3个方位分别检测单开3#机和单开2#机的噪声频谱(表2),3#机倍频带消声效果均优于2#机,2kHz以上高频段降噪效果更明显,4kHz降幅达最大值-23.7%。
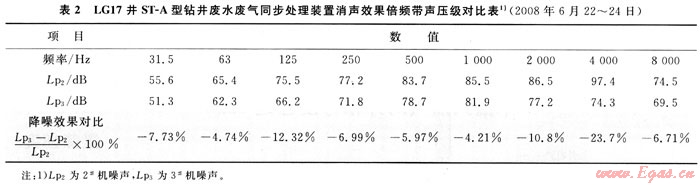
3 环境效益与经济效益
钻井废水废气同步消减技术具有源头消减废水和柴油机排气污染物、消声降噪减阻和减少柴油机功率损耗等多方面效益。本文仅以钻井废水源头治理效果分析其环境效益和经济效益。
3.1 废水源头治理、提高环保水平
该技术回收利用柴油机排气废热消减钻井废水,不外加任何物质与能量,与化学处理或外运、回注等方法相比,具有如下显著优势:
1) 废水消减与钻井作业同步进行日集日清。
2) 单机实测平均消减钻井废水0.517m3/h,即平均12.4m3/d(24h),大于目前井场钻井废水产生量,可以确保废水不外排、不外运、不累积,进行源头治理。
由此可见本技术环境效益显著,尤其对既不具备废水回注条件、又不便于长距离运输的钻井作业区建立废水零排放清洁生产体系具有重大意义。
3.2 减少征地、降低成本
以LG气田5000~6000m深井为例,目前三废池总池容约2500m3(废水池约占50%),征地及基建投资约80万元。钻井作业期120~150d,产生废水总量900~1200m3。原有处理方法是部分外运集中处理,部分在现场随废浆废渣固化,平均处理成本超过200元/m3。以上合计单井费用超过100万元。
本技术装置设计使用年限5年,单井摊销费用低于10万元,且处理过程不加药,运行管理费显著低于其他方法。该技术可以保障钻井废水日集日清,废水池功能仅为短周期循环,可使其总容积缩减1/3,从而大幅度减少井场征地与基建投资。由此,采用本技术对钻井废水进行源头治理,与现有技术相比可以节约成本30%~50%,产生显著的经济效益。
4 结论
1) 利用柴油机排气废热消减钻井废水,190型钻井柴油机单机在额定工况(1300r/min)下消减废水理论值为649kg/h、实测值(1200r/min)为538kg/h,并且消减排气烟尘。
2) 钻井废水废气同步消减装置的降噪功能比原有柴油机排气消声器提高4.2%0~23.7%,同时使排气背压降低70%以上,功率损失比减小至少1%。
3) 钻井现场示范运行结果表明,该技术实现了钻井废水源头治理,对不具备回注条件、不便于长距离运输的钻井作业区建立废水零排放清洁生产体系意义重大。
参考文献
[1] EKINS P,VANNER R,FIREBRACE J.Zero emissions of oil in water from offshore oil and gas installations:economic and environmental implications[J].Journal of Cleaner Production,2007,15:1302-1315.
[2] AI,AJMI HAMAD,AL-JADI LSSA,AL-RUHAIMANI FERAS.et al.Effluent water disposal experiences in the Greater Burgan Field of Kuwait[C].International Petroleum Technology Conference,2007,Dubai,U.A.E.SPE 11551.
[3] GAUDLIP A W,PAUGH L O,HAYES T D.Marcellus shale water management challenges in Pennsylvania [C].SPE-Shale Gas Production Conference,2008,Fortworth,Texas,USA.SPE 119898.
[4] 张雷,欧阳峰,廖千家骅.我国钻井废水处理研究进展[J].中国环保产业,2007(6):30-34.
[5] 黄志宇,鲁红升,李建波,等.气井钻井废水深度处理实验研究[J].天然气工业,2005,25(5):44-46.
[6] 熊春平,朱权云.钻井废水处理工艺评价[J].石油与天然气化工,1997,26(1):61-64.
[7] 李新华.依靠装备科技进步做好节能减排工作[J].国际石油经济,2008,16(5):31-34.
[8] 夏小全,朱家骅,夏素兰,等.钻井废水、废泥浆和发动机废气现场综合处理方法:中国,101244848A[P].2008-08-20.
[9] 《化学工程手册》编辑委员会.化学工程手册:第4卷[M].北京:化学工业出版社,1989:15-30.
[10] 郑郧.低能耗低成本排气消声器的研制[J].环境工程,2000.18(3):39-41.
(本文作者:朱德浩1 周勇1 夏素兰1 夏小全2 向启贵3 易畅3 凌立苏4 1.四川大学化工学院;2.中国石油西南油气田公司工程技术监督中心;3.中国石油西南油气田公司安全环保与技术监督研究院;4.中国石油新疆油田公司勘探公司)
您可以选择一种方式赞助本站
支付宝转账赞助
微信转账赞助