摘 要:利用通用分析软件ABAQUS,应用 “生死单元” 技术,模拟了基坑开挖、 填埋过程对Φ1 620 mm×20 mm 大直径埋地管线应力应变的影响。 通过对不同埋深管体应力应变的有限元分析,得出施加内压2.5 MPa,埋深8 m 时,管体受到的等效应力最大 (130 MPa),未超过材料的屈服强度,管体并未发生塑性变形,管体横向最大位移为2.47 mm。 通过理论计算校核,埋深8 m 时,管体水平方面最大变形量为12.5 mm,远小于标准规定的48.6 mm,管体径向稳定性可靠。
0 引 言
目前,大直径埋地管道在施工安装时,导致坑内土体卸载,使土体初始应力场状态破坏,土体内应力重新分布,管道安装完成后,重新回填土体,由于土体的重力作用,会使管体结构发生变形、 位移,对地下管线及地下设施带来不利影响[1-4]。 随着管道直径的增加,其径厚比增大,径向稳定性变差,因此研究埋深对管道应力应变影响就显得十分关键。 国内外学者对管道受断裂、 挤压的研究较多,但是对大直径管道安装后土体对其应力应变影响的分析较少[5-8]。 大直径管道其变形模式更趋于压力容器,传统的输送管道应力校核管道模型不再适用,因此研究土体对管道应力应变的影响具有重要的现实意义。
本研究以某市的热力管道为对象,利用 “生死单元” 技术,对土体开挖过程以及钢管不同埋藏深度进行有限元模拟,从而完成对大直径埋地管道径向变形的预测,并与理论值进行对比,为管线设计及管线安全运营服役提供一定的理论指导和技术支持。
1 土体和管道物理模型
以规格为 Φ1 620 mm×20 mm、 L360M 材质的输送管为研究对象,利用ABAQUS 有限元分析软件,分别模拟埋深为 2 m、 5 m 和 8 m,工作压力为2.5 MPa 时,地应力和内压载荷对管道截面应力、 应变的影响。 L360M 钢Φ1 620 mm×20 mm 输送管道的性能参数见表1,土体性能参数见表2。
表1 L360M 钢Φ1 620 mm×20 mm 管道的性能参数

表2 土体性能参数

2 有限元模型的建立
建立12.5 m×25 m 的土体模型,相对于管体的尺寸,土体面积相当于无限大。 有限元分析采用ABAQUS 软件,采用2D 平面模型进行分析。管体以及埋藏深度均应用平面应力单元,总单元数为 8 020 个,节点数 7 636 个。 土体底部施加y 方向的对称约束。 土体顶部为自由端,土体左侧和右侧施加x 方向的对称约束。 管内壁施加均匀的胀管压力。 不考虑温度载荷的作用,管体不同埋深条件下的有限元模型如图1 所示。
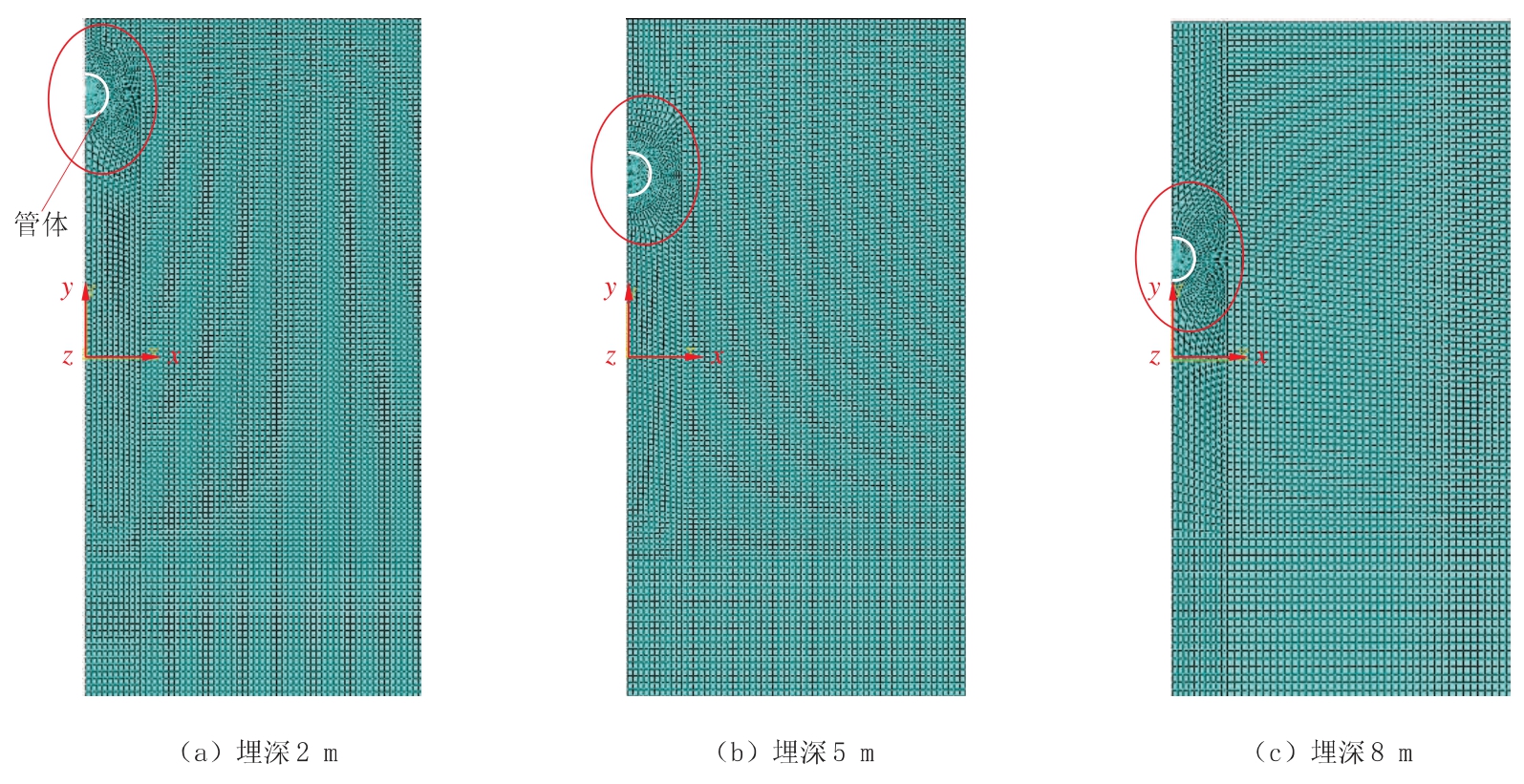
图1 管体不同埋深条件下的有限元模型
2.1 弹塑性有限元计算
本研究假设材料遵循弹塑性和线性本构模型,并且以Von Mises 屈服准则为评判标准。 利用 “生死单元” 技术模拟土体从 “无” 到 “填充管体顶部”,到最终的完全填满管体过程。
2.2 载荷施加
由于管体在施工安装时,需经历开挖、 埋管、 回填土等过程,因此在不同的开挖过程中所受的应力应变不同,对于管体在地底下所经历的应力应变过程,不考虑内压,需要分4 个连续载荷阶段: ①开挖前整个土体的地应力场的载荷施加;②不同深度管道埋置处土体开挖,开挖后土体应力场的变化;③管道置入后,施加重力载荷对管体以及土体应力应变场的影响;④土体回填后,施加重力载荷对管体以及土体应力应变场的影响。
为了确保计算收敛并获得足够精确的计算结果,载荷是通过逐渐递增的载荷增量RAMP 方法施加的,即通过多个子载荷步将施加的压力逐渐加到预定的加载压力值。
3 有限元结果分析
3.1 土体地应力场分布
在建好有限元模型后,开挖前首先对土体施加重力载荷,生成地应力场分布如图2 所示。
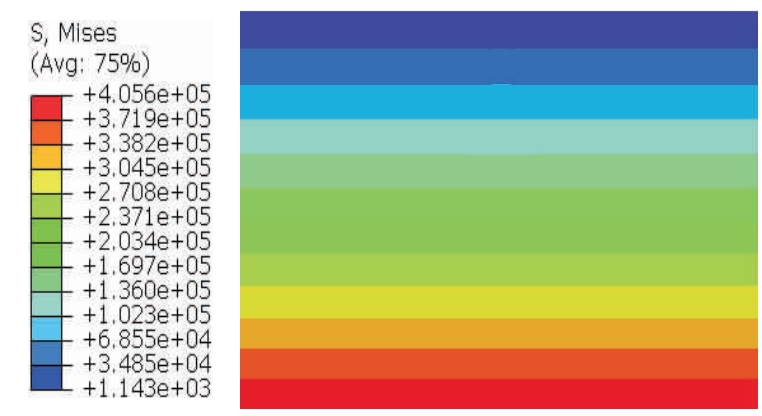
图2 土体地应力场分布
3.2 土体开挖过程中应力场分布
采用 “生死单元” 技术模拟土体开挖,壕沟深度为2 m、 5 m 和8 m。 开挖壕沟的土体应力应变场分布如图3 所示。
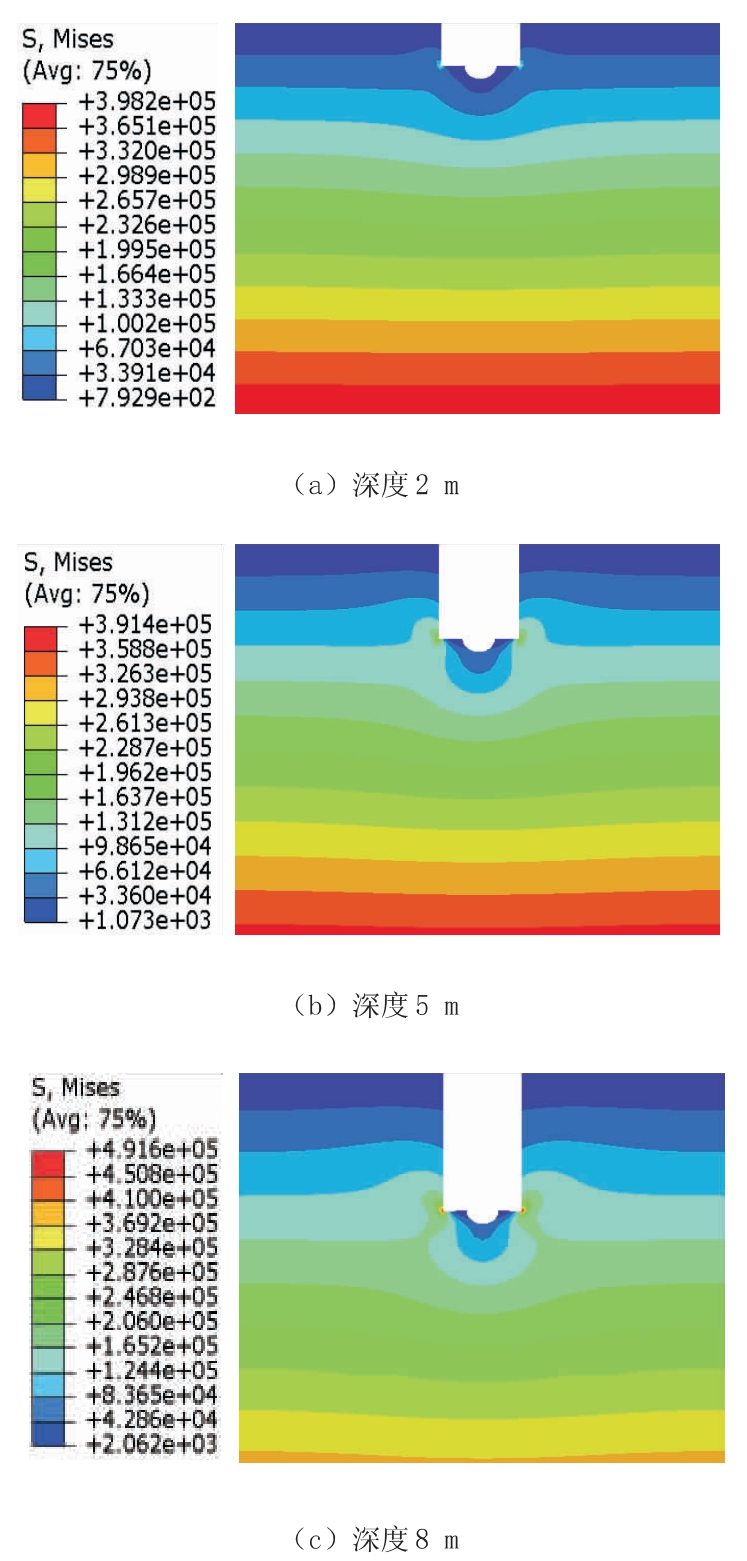
图3 土体开挖不同深度时的应力场分布
3.3 管道安装后应力应变分布
不同埋深下管体的应力场分布云图如图4所示。 由图4 可见,埋深 2 m 时管体应力最大值为 8.37 MPa,埋深 5 m 时管体应力最大值为 11.6 MPa,埋深 8 m 时管体应力最大值为14.9 MPa。 三者的应力分布云图趋势基本一致,管体左右两侧靠近壕沟处应力较大,主要是由于开挖后壕沟处土体向内侧挤压导致。 可以看出,随着埋深的增加,管体的应力逐渐增大,应力分布趋势基本一致。
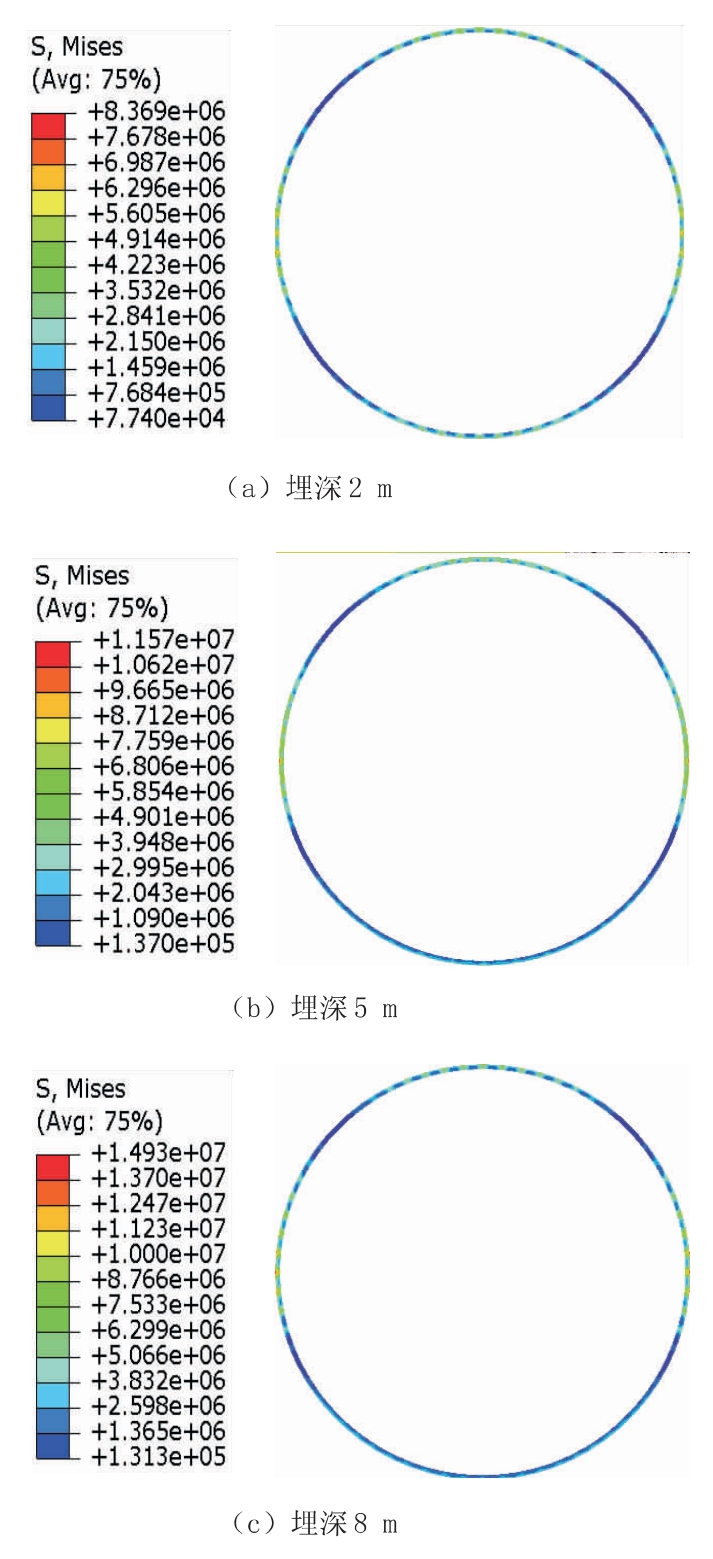
图4 不同埋深下管体的应力场分布云图
3.4 回填土体重力载荷加载
不同埋深下回填土体后管体的应力场分布云图如图5 所示。 从图5 可见,回填土体后,埋深2 m 的管体受到的最大等效应力为21.4 MPa,埋深5 m 的管体受到的最大等效应力为36.98 MPa,埋深8 m 的管体受到的最大等效应力为56.6 MPa,均未超过材料的屈服强度,管体并未发生塑性变形。 可以看出,随着埋深的增加,管体受到的应力逐渐增大,应力主要集中在管体左右两侧以及顶部和底部。
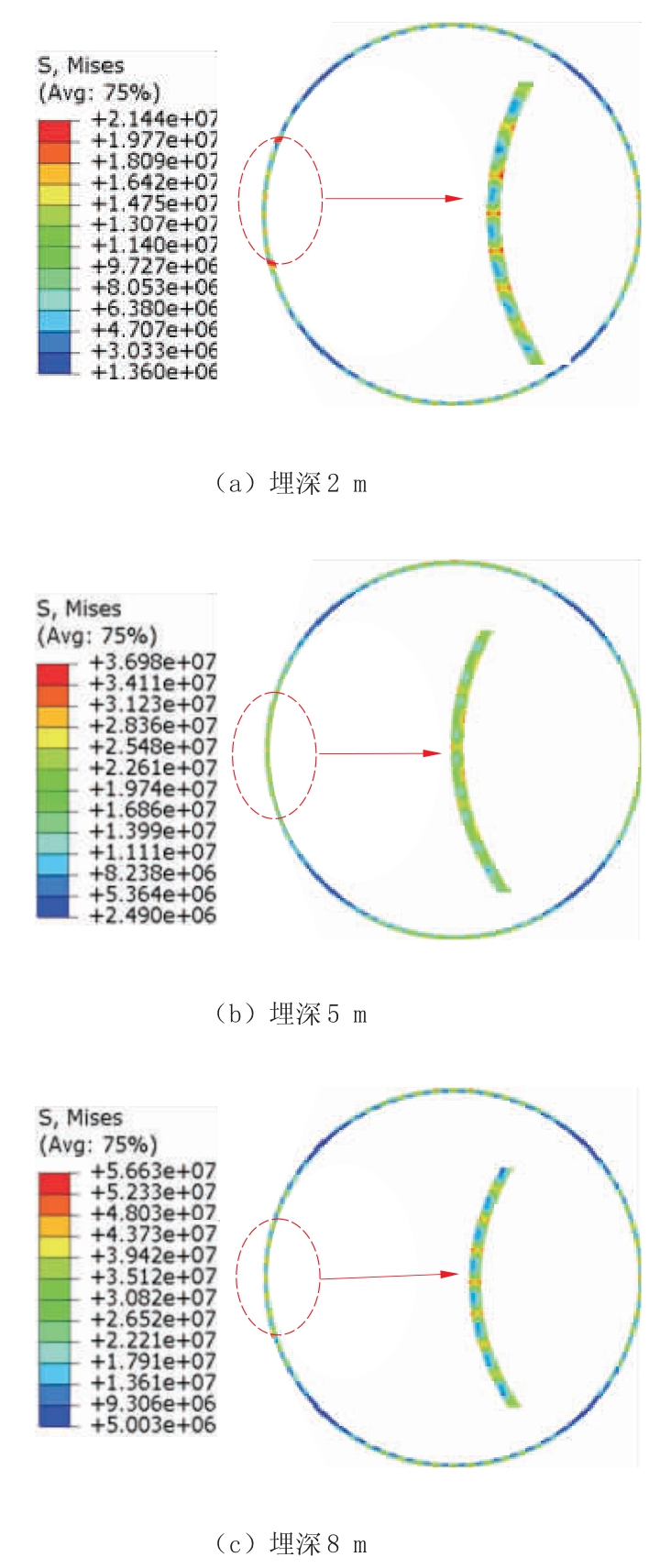
图5 不同埋深下回填土体后管体的应力场分布云图
3.5 不同埋深回填土体后管体位移场分布
不同埋深下管体x 方向应变分布云图如图6所示。 从图6 可见,埋深 2 m、 5 m 和 8 m 时,x 方向的最大位移即最大变形分别为1.16 mm、1.98 mm 和2.47 mm。 随着埋深的增加,管体受到的径向位移逐渐增大,径向变形主要集中在管体左、 右两侧。 y 方向的位移主要来自土壤自身的变形和钢管受土体的作用力后发生的变形。
在管体上选取一条路径Path1,对管体上的应力及位移作定量分析,结果如图7 所示。
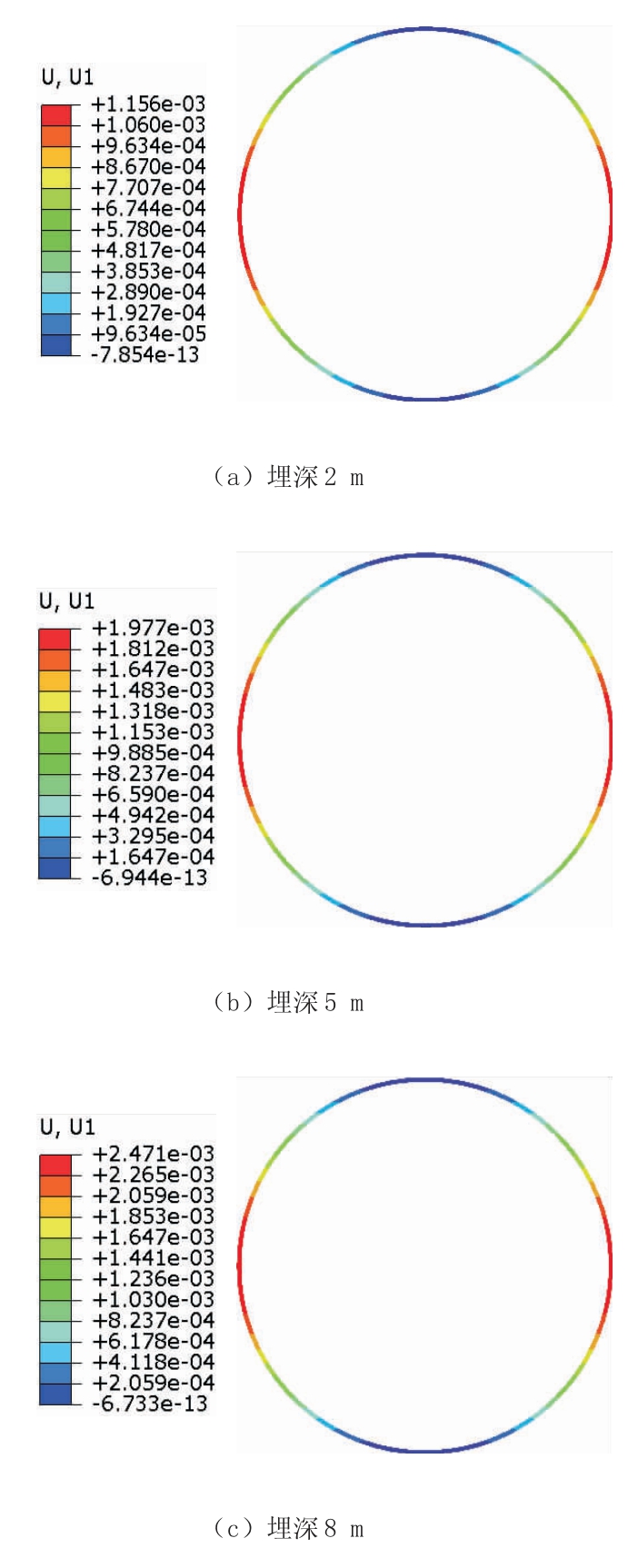
图6 不同埋深下管体x 方向应变分布云图

图7 沿管体路径Path1 的应力及位移
沿着路径 Path1,埋深为 2 m、 5 m 和 8 m的管体等效应力曲线如图8 所示。 由图8 可见,路径Path1 起始端和末端的等效应力较大,路径中间部分应力较小,埋深为8 m 的整体应力变化幅度较大,最大等效应力为 130 MPa,埋深5 m 的管体等效应力变化幅度次之,埋深为2 m的管体等效应力变化幅度最小。
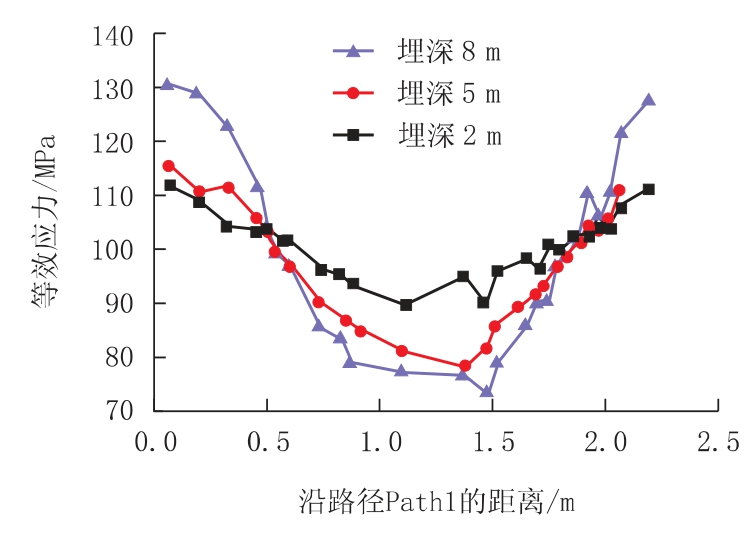
图8 不同埋深下管体的等效应力曲线
沿着路径 Path1,埋深为 2 m、 5 m 和 8 m的管体位移曲线如图9 所示。 由图9 可见,起始端和末端的水平位移较小,路径中间部分x 方向的位移较大,埋深为8 m 的整体水平位移变化幅度最大,埋深5 m 的整体水平位移变化幅度次之,埋深为2 m 的管体水平位移变化幅度最小。 y 方向位移起始端位移相对于末端位移要大,路径中间部分y 方向位移变化幅度较小,主要是因为管体中间两侧受到土体的挤压作用。
不同埋深下管体的位移分布如图10 所示。从图10 可见,不同管体的最大x 方向位移随着埋深的增加而增大,管体的最大y 方向位移随着埋深的增加而减小。 这主要是由于埋深越深,土体的重力作用幅度越大,管体节点在y方向运动的幅度小的缘故。
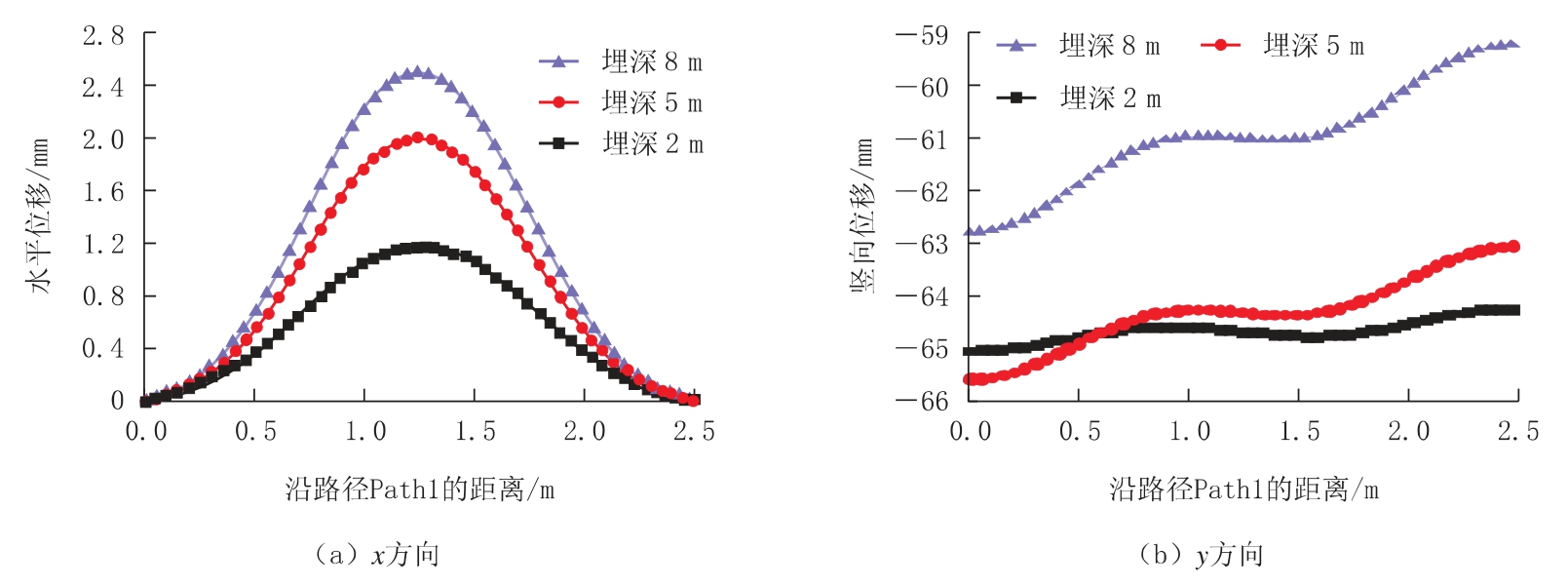
图9 不同埋深下管体的x 方向和y 方向位移曲线
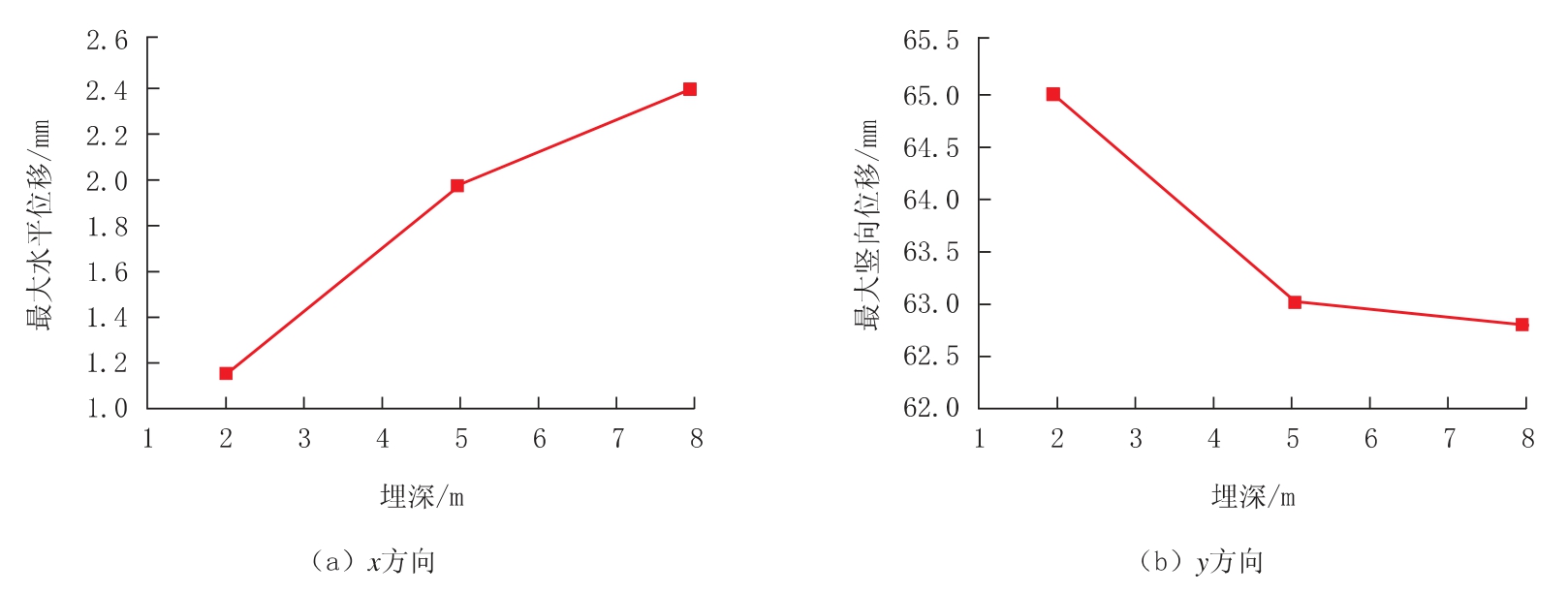
图10 不同埋深下管体的位移分布
4 理论计算结果分析
在长输管道设计时,某些地段管线埋深会较深,在此种情况下,需要对管线的径向稳定性进行验算。 管道的径向稳定性一般按无内压状态进行校核。
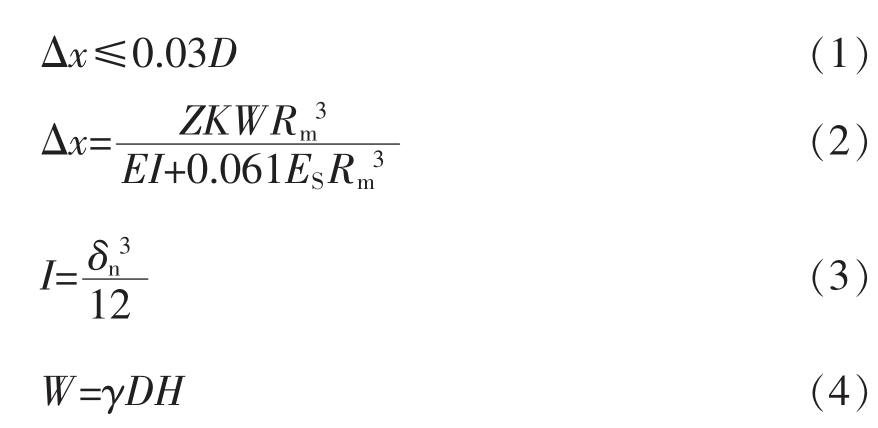
式中: D——钢管外径,m;
Δx——钢管水平方向最大变形量,m;
Rm——钢管平均半径,m;
W——作用在单位管长上的总竖向荷载,MN/m;
Z——钢管变形滞后系数,取1.5;
K——基座系数,取0.103;
E——管材弹性模量,取2.05×105 N/m2;
I——单位管长截面惯性矩,m4/m;
δn——钢管公称壁厚,m;
ES——回填土壤的变形模量,MPa;
γ——土壤容重,取0.016 7 MN/m3;
H——管顶回填土高度,m。
管道径向稳定性校核计算结果见表3。
表3 管道径向稳定性计算结果
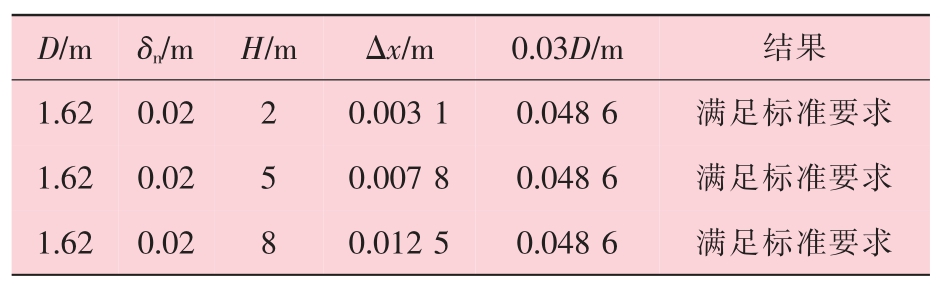
通过管道稳定性的理论计算,当埋深为2 m、5 m 和8 m 时,管道径向最大变形分别为3.1 mm,7.8 mm 和12.5 mm,远远小于标准要求的0.03D(48.6 mm)。 有限元分析结果得出,未考虑内压力,埋深 2 m、 5 m 和 8 m 时,x 方向的最大位移即最大变形分别为 1.16 mm、 1.98 mm 和 2.47 mm,也远小于标准要求的0.03D (48.6 mm)。 理论计算与有限元分析结果相比,计算结果偏大,主要是由于此理论计算公式是管道径向稳定性验算校核采用,故计算结果要留有较大裕量,确保管道设计的安全可靠。 研究管道稳定性的理论计算时,为保证与有限元计算的对比,采用的回填土壤变形模量与输气管线设计标准中规定的土壤变形模量有差别,本研究为大直径埋地管道的应力应变分析研究提供一种新思路,不作为埋地管道设计安装的依据。
5 结 论
(1) 埋深 2 m 时,地应力对管体产生的最大等效应力为21.4 MPa;埋深5 m 时,地应力对管体产生的最大等效应为36.98 MPa;埋深8 m 时,地应力对管体产生的最大等效应力为56.6 MPa,均未超过材料的屈服强度,管体未发生塑性变形。
(2) 通过理论计算校核,埋深为 8 m 时,管体最大变形量 (弹性变形) 为12.5 mm,远小于标准规定的48.6 mm。
(3) 通过理论计算校核和有限元分析方法确定,埋深为8 m 时,管体径向稳定性安全可靠。
[1]刘爱文,胡聿贤,李小军,等.大口径埋地钢管在地震断层作用下破坏模式的研究[J].工程力学,2005(3):82-87.
[2]肖成志,王嘉勇,杨爱克.静载作用下埋地管道数值模拟及其力学性能分析[J].防灾减灾工程学报,2018,38(1):22-29.
[3]刘阳阳.地下管道爆炸对埋地管网的毁伤数值模拟[D].南京:南京理工大学,2016.
[4]邵煜.埋地管道的失效机理及其可靠性研究[D].杭州:浙江大学,2008.
[5]黄雄.爆破荷载作用下埋地钢管的动力响应研究[D].武汉:武汉科技大学,2018.
[6]翁多斯.地铁振动对埋地燃气管道的影响研究[D].成都:西南交通大学,2016.
[7]谭建为,梁光川,罗勇.跨断层埋地管段数值模拟分析研究[J].石化技术,2017,24(10):103-103.
[8]赵新威,曾祥国,姚安林,等.地震载荷作用下埋地输气管道的数值模拟[J].石油机械,2014,42(3):4-109.
[9]孙乃波,陈胜宏.生死单元在拱坝施工仿真分析中的应用[J].水电能源科学,2004,22(3):65-67.
[10]吴建东,许健.ANSYS 有限元生死单元技术在砼面板堆石坝渗流计算中的研究与应用[J].甘肃农业大学学报,2011,46(3):142-146.
[11]李伟,易壮鹏.基于ANSYS 生死单元的移动荷载作用下桥梁结构动力响应分析[J].公路与汽运,2018(2):118-121.
[12]牟淑志,杜春江,牟福元.基于 RAMP 和ANSYS 二次开发的结构拓扑优化[J].机械工程师,2010(1):59-61.
[13]张永亮,徐聪,陈兴冲.城市曲线匝道桥有限元建模及抗震性能评估[J].兰州交通大学学报,2013,32(1):1-4.
[14]周国强.基于无网格法的各向异性材料传热分析及拓扑优化研究[D].湘潭:湘潭大学,2017.
[15]张永亮,徐聪,陈兴冲.城市曲线匝道桥有限元建模及抗震性能评估[J].兰州交通大学学报,2013,32(1):1-4.
Stress-strain Finite Element Analysis and Calculation of Large Diameter Buried Pipeline
您可以选择一种方式赞助本站
支付宝转账赞助
微信转账赞助