摘要:近年来我国油气管道腐蚀现象日趋严重,对腐蚀管道进行剩余强度评价可以有效地避免和预防管道泄漏事故的发生。1984年美国机械工程师协会颁布的ASME B31G—1984标准是研究腐蚀管道剩余强度评价方面使用最广泛、最基本的评价标准之一,之后又推出了ASME B31G—1991修改版及改进的RSTRENG方法。为此,重点介绍了最新版ASME B31G—2009标准的分级评价方法以及较之前两版ASME B31G的先进性。根据收集到的67组管道全尺寸爆破试验数据,分别利用新旧ASME B31G标准和RsTRENG方法计算得出预测失效压力,并与实际爆破压力进行了比较。通过实例验证和对比分析可知:新版ASME B31G—2009采用4个等级进行腐蚀管道的剩余强度评价,更便于评价人员根据现场操作难易程度、资料详细程度以及评价精度等要求选择不同的评价等级进行操作;其保守性明显降低,预测结果更加接近真实值,具有较强的实用性;但与RSTRENG相比,它仍存在一定的保守性。另外,新版ASME B31G—2009仍不适于评价大口径、高强度的管道,在评价范围方面有待进一步提高。
关键词:天然气管道;腐蚀;缺陷;剩余强度评价ASME;B31G;RSTRENG;评价标准
近年来,世界各国的油气管道因腐蚀所导致的失效事故频繁发生,造成能源的浪费以及环境的破坏,严重时给社会造成了巨大的财产损失。对管道进行剩余强度评价可以有效地降低甚至避免管道失效的发生。从20世纪60年代末开始,世界各国一直在进行腐蚀管道剩余强度评价方面的研究,颁布了许多相关的评价标准及规范。1984年美国机械工程师协会(ASME)颁布了ASME B31G—1984标准,其前身是基于断裂力学的NG-18表面缺陷计算公式[1],它是后来许多相关评价标准的基础,至今仍是使用范围最为广泛的评价腐蚀管道剩余强度的标准之一。随着世界工业水平的飞速发展,继最初的ASME B31G—1984版在1991年进行了一次修改后,2009年对该标准又进行了一次修改,笔者主要针对最新版ASME B31G—2009的先进性进行分析。
1 新版ASME B31G—2009介绍
1.1 ASME B31G—2009分级评价方法
新版ASME B31G—2009标准延续并完善了原始的ASME B31G评价方法,其最大的变化是采用分级评价的理念,由保守到精确,由粗略到精细,层层深入。评价共分为4个等级,各个等级之间不是孤立存在的,而是按照实际操作的难易程度、评价结果的精确性和保守性而制定的由初级到高级的评价原则。有利于评价人员根据现场操作难易程度、资料详细程度以及评价精度等要求选择不同的评价等级进行操作,大大提高了工作效率和评价结果的精确度,具有很强的实际应用价值。
1.1.1零级评价
根据给定的管道直径、壁厚和腐蚀坑深度在表1中查取现成的腐蚀区域最大腐蚀长度数据,用于确定连续相邻的腐蚀区,或一串相互作用的金属损失区的长度,步骤如下[2]:①根据相关记录或直接测量确定管道的直径和壁厚;②通过相关记录确定管材的材料属性;③清理管道表面的腐蚀至露出金属表面,当清理带压腐蚀管道表面时需要多加小心;④测量腐蚀区最大深度(d)和腐蚀区轴向距离(L);⑤确定与管道外径(D)相关的附表;⑥在附表上,找出与腐蚀部位的最大测量深度相等的那一行,如果表中没有恰当的测量深度值,可以选择邻近的较大深度那一行;⑦沿横向找到管道壁厚(t)的那一列,如果该壁厚没有列出,即可选取邻近的较薄壁厚那一列。壁厚的列与腐蚀深度的行交叉点处即为腐蚀区域允许的轴向长度(L);⑧如果管道上金属腐蚀区域的轴向长度(L)不超过表中所给的值即为可行。
当腐蚀深度比大于管道壁厚的10%且小于80%的邻近腐蚀区域,腐蚀区的轴向长度不得大于由下式计算出的距离:
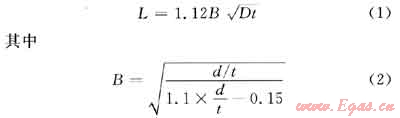
B不能超过4.O。如果腐蚀深度在10%~17.5%之间,则式(1)中B=4.0。
零级评价实际操作起来比较简单,便于现场操作人员实际应用,但缺点是比较保守。如果没有通过零级评价可以进行下一级评价。零级评价基本上沿用了原始B31G的方法,只是改用了公制单位。
1.1.2一级评价
根据测量金属损失的最大轴向长度和深度,进行较复杂的计算。一级评价需要该领域的工程师、腐蚀技术人员、涂层检验员或其他受过相关培训的人员进行操作。步骤为:①根据相关记录或直接测量确定管道的直径和壁厚;②清理管道表面的腐蚀产物至露出金属表面,当清理带压腐蚀管道表面时应小心;③测量腐蚀区域最大深度(d)和轴向长度(L);④根据相关记录确定适用管材的材料属性;⑤选择如下失效准则计算失效应力(SF);⑥规定一个可接受的安全系数SF;⑦比较SF和SF·SO当SF≥SF·SO时,缺陷可以被接受。
当z≤50时,为短缺陷:
M=(1+0.6275z-0.003375z2)1/2 (3)
当z>50时,为长缺陷:
M=0.032z+3.3 (4)
失效应力表达式为:
SF=Sflow{[1-0.85(d/t)]/[1-0.85(d/t)/M]} (5)
其中z=L2/Dt Sflow=1.1·SMYS
式中SO为最大操作压力下的环向应力;Sflow为流变应力;M为鼓胀系数。
1.1.3二级评价
使用有效面积法,操作步骤与一级评价相似,不同的是有效面积法需要详细测量管道腐蚀深度或剩余壁厚,更贴近实际的腐蚀情况。有效面积法的预测失效应力的表达式如下:

有效面积法是分别对腐蚀剖面内的一系列矩形截面计算出相关段的失效压力,把最小的失效压力作为管子的失效压力。该方法需要细致的测量,必须沿着管子长度方向进行大量的测量,以确定详细的腐蚀剖面图。因计算量很大,有必要采用PC程序。
1.1.4三级评价
以上3个等级的评价都没有通过或需要考虑更复杂的情况时应考虑进入三级评价。该等级评价采用更加详细的分析方法,如有限元分析方法[3~5]等。分析考虑到影响结果的多种因素包括:载荷、外力、边界条件、约束、变形、材料的应力一应变曲线等。
1.2 新版ASME B31G—2009的先进性
新版ASME B31G—2009针对前两版ASME B31G的保守性作了如下改进:①分级评价:新版B31G—2009首次提出分级评价的理念,4个评价等级有机结合起来,操作过程由简到繁,考虑的评价条件越来越详细,评价结果也是由保守到精确。②缺陷面积:新版B31G的一级评价将缺陷面积定义为0.85dL,该值介于矩形面积和抛物线形面积之间。降低了前两版B31G[6~7]的保守性。二级评价中采用有效面积法,实际详细测量管道腐蚀深度或剩余壁厚,更贴近实际的腐蚀情况,评价结果也更加精确。③长、短缺陷临界值(z):鉴于原B31G的保守性,将长、短缺陷的临界值由20上调到50。④鼓胀系数(M):新版B31G根据长、短缺陷的不同情况分别定义了不同的M值表达式。⑤失效准则:设定了基于缺陷面积为0.85dL的统一的失效应力(压力)表达式(式5)。
2 ASME B31G与RSTRENG对比分析
2.1 RSTRENG与ASME B31G方法比较
RSTRENG方法是在原始ASME B31G的基础上,针对831G的保守性进行改进获得的,包括RSTRENG 0.85dL和RSTRENG有效面积法两种评价方法,主要对孤立缺陷进行评估[8]。新版ASME B31G—2009的一级评价和二级评价分别参照了RSTRENG的0.85dL面积法和有效面积法并进行了改进。表2总结了它们的联系与区别。
2.2 实例验证
本文参考文献[9]中对比分析了前两版B31G,并得出结论:修正版ASME B31G—1991比原版ASME B31G—1984的保守性有所降低,预测结果更贴近实际值,但仍有不小的安全裕量。在前人研究的基础上笔者根据本文参考文献[10]中收集到的67组实验数据,利用ASME B31G—1991、ASME B31G—2009(一级评价)和RSTRENG 0.85dL3种方法计算预测失效应力,分别与真实值进行误差比较,结果见图1。
由图1可知,新版ASME B31G—2009比ASME B31G—1991的保守性有所降低,预测结果更贴近真实值。然而,与RSTRENG 0.85dL相比,新版ASME B31G—2009仍存在一定的保守性,仍有改进空间。需要注意:RSTRENG 0.85dL和ASME B31G标准均只适用评价中低强度等级管道,在评价中高强度等级管道时均出现不安全现象。
2.3 RSTRENG与ASME B31G—2009实用性分析
RsTRENG与AsME B31G—2009中各等级评价方法预测结果的保守性与实际操作的难易程度都不尽相同。图2将这些评价方法按它们的保守性和可操作性进行排序,更便于管道评估人员根据实际情况选择适合的评价方法进行管道剩余强度评价。图2中的各级评价方法保守程度随着箭头逐渐降低,而操作难度则随着箭头逐渐增大。
3 结论及建议
1) 新版ASME B31G—2009采用的分级评价方法便于评价人员根据现场操作难易程度、资料详细程度以及评价精度等要求选择不同的评价等级进行操作。大大提高了工作效率和评价结果的精确度,具有很强的实用价值。
2) 与前两版ASME B31G相比,新版ASME B31G—2009的保守性大大降低,预测结果更加精确。
3) 通过与RSTRENG进行实例验证和实用性比较可以看出:新版ASME B31G—2009仍存在一定的保守性,有进一步改进的空间。
4) 新版ASME B31G—2009在适用钢的等级方面有待进一步完善,应考虑评价高强度等级、大口径管道的剩余强度评价的需要。
参考文献
[1] 帅健,张春娥,陈福来.基于爆破试验数据对腐蚀管道剩余强度评定方法的验证[J].压力容器,2006,23(10):5-8.
[2] ASME B31G—2009.Manual for determining the remaining strength of corroded pipelines[S].American Society of Mechanical Engineers,2009.
[3] 帅健,张春娥,陈福来.非线性有限元法用于腐蚀管道失效压力预测[J].石油学报,2008,29(6):933-937.
[4] 张鹏,段永红.长输管线风险技术的研究[J].天然气工业,1998,18(5):72-76.
[5] 陈正阁,王长龙,纪凤珠.基于有限元法的输气管道漏磁场分析[J].天然气工业,2007,27(2):111-113.
[6] ANSI/ASME B31G—1984.Manual for determining the remaining strength of corroded pipelines[S].New York:1984.
[7] ASME B31G—1991.Manual for determining the remaining strength of corroded pipelines[S].American Society of Mechanical Engineers,1991.
[8] 王禹钦,王维斌,冯庆善.腐蚀管道的剩余强度评价[J].腐蚀与防护,2008,2(1):28-31.
[9] 帅健,张春娥,陈福来.腐蚀管道剩余强度评价方法的对比研究[J].天然气工业,2006,26(11):122-125.
[10] 帅健.管线力学[M].北京:科学出版社,2010:23-25.
(本文作者:马彬1 帅健1 李晓魁2 王俊强1 冯庆东1 1.中国石油大学(北京)机械与储运工程学院;2.中国石油管道公司兰州输气分公司)
您可以选择一种方式赞助本站
支付宝转账赞助
微信转账赞助