摘要:针对城镇集中供热锅炉房的特点,提出使用钙基脱硫剂的双液位喷射鼓泡烟气脱硫除尘装置。介绍了双液位喷射鼓泡烟气脱硫除尘装置的脱硫机理,实验分析了脱硫剂pH值对脱硫效率的影响、冲击管出口烟气流速对烟气压力降的影响,探讨了该脱硫装置的工业应用。使用钙基为脱硫剂的双液位喷射鼓泡烟气脱硫除尘装置,可减缓设备结垢,降低脱硫除尘成本,实现脱硫产物随灰渣一同处理。
关键词:双液位;喷射鼓泡;烟气脱硫除尘
Double Liquid-level Jet Bubbling Flue Gas Desulfurization and Dust Removal Device
PENG Tie-cheng
Abstract:Aimed at the characteristics of centralized heat-supply boiler room in cities and towns,a double liquid-level jet bubbling flue gas desulfurization and dust removal device using calcium-based desulfurizer is presented. The desulfurization mechanism of this device is introduced. The effect of pH value of desulfurizer on desulfurization efficiency as well as the effect of flue gas velocity at the outlet of impact tube on flue gas pressure drop are experimentally analyzed. The industrial applications of this device are discussed. This device can ease device scaling and reduce cost and achieve simultaneous treatment of desulfurization product and ash.
Key words:double liquid-level;jet bubbling;flue gas desulfurization and dust removal
1 概述
我国是世界上工业锅炉数量和耗煤量较多的国家。工业锅炉的特点是热功率小、排放点分散,在我国北方地区多用于供热,因此供暖期内,SO2成为大气中主要污染物,烟气脱硫是目前减少SO2排放的主要手段。近年来工程技术人员针对工业锅炉烟气脱硫做了大量工作,并相继对氧化镁法[1~3]、氨法[4]、双碱法[5、6]做了大量的研究工作和分析报道。氧化镁法、氨法的核心在于脱硫产物的回收和利用,对于管理水平较高、设备完善的电力锅炉和大型工业锅炉烟气脱硫效果是令人满意的。但在众多工业锅炉烟气脱硫的应用中,由于管理水平低或缺少脱硫产物的回收设备,造成废水排放中含有大量硫酸盐和亚硫酸盐,将气态污染转化为水体污染。双碱法理论上是将烟气中二氧化硫转化为硫酸钙和亚硫酸钙,是一种减少污染预防设备结垢的方法,使用过程中若要保证一定的脱硫率,液气比要大于2,而且脱硫剂pH值不能过高。但在实际应用过程中由于许多用户不能保证较高的脱硫剂循环量,只能提高脱硫剂的pH值,造成设备和管道结垢,最终导致脱硫失效。
国内技术人员在日本千代田公司开发的CT-121喷射鼓泡反应塔工艺[7]基础上,利用喷射鼓泡技术对烟气脱硫进行了分析研究[8~10]。实践证明,该技术在负荷稳定的环境中,工作可靠,脱硫效率高,实现有效脱硫和稳定运行[11、12]。为了满足工业锅炉烟气有效脱硫的需要,本课题组开发研制了双液位喷射鼓泡烟气脱硫除尘装置,使用钙基脱硫剂,实现脱硫产物随灰渣一同排放,不产生含硫酸盐废水。本文对双液位喷射鼓泡烟气脱硫除尘装置的实验研究及工业应用进行探讨。
2 脱硫除尘机理
双液位喷射鼓泡烟气脱硫除尘装置根据撞击流原理,强化过程的热质传递以促进化学反应[11]。其机理是通过惯性碰撞和离心撞击与拦截,强化烟气脱硫除尘效果。低液位、高液位的工作流程见图1、2。
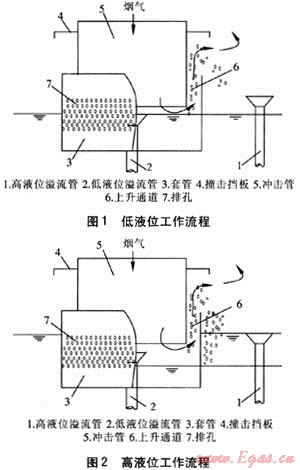
含尘烟气进入冲击管,冲击液面,质量大的烟尘接触液面被捕集,烟气转向通过由冲击管和套管形成的通道向上流动,在通道内流速提高,静压减小,套管外部液体被引射通过套管的排孔流入通道内与上升气流激烈混合后被加速。烟气中的烟尘在与液体混合过程中被加湿、粒化,烟气中的二氧化硫在与脱硫剂混合过程中被中和吸收。液气混合物流出上升通道遇撞击挡板后液滴与气体分离,气流向上流动,液滴流回液面。通过排孔进入上升通道的液体的量与气流速度的变化规律一致,即烟气速度越高,产生的静压越低,引射的水量越大。
引风机停运时,液位由低液位溢流管控制,低液位溢流管保证冲击管与液位之间有一定空间,供工业炉封火状态时烟气通过。当引风机开启后烟气量逐渐增大,套管内液位低于低液位溢流管,此时低液位溢流管失效,套管外液位由高液位溢流管控制,脱硫剂循环通过高液位溢流管进行。
正常工作时,烟气流出冲击管转向流动时,在液面上部空间,动压转化为静压,在液面上部排孔两侧产生压差,烟气通过排孔进入液相形成鼓泡,远离液位的排孔压差较大,鼓泡剧烈。形成鼓泡的烟气量与开孔率、套管两侧的压力差有关,进入上升通道的烟气量与进入上升通道的液体量及流速有关,通过排孔形成鼓泡的烟气阻力与进入上升通道的烟气阻力是相当的。进入上升通道的烟气量与通过排孔形成鼓泡的烟气量的比例是通过烟气压力降来平衡的,即与开孔率、液气比、气流速度、高液位溢流管的安装位置有关。
低负荷时烟气量较少,烟气流动阻力小,低液位溢流管循环工作,液位与冲击管出口处空间较小。因此烟气横掠液面流速达到8m/s时就能卷吸液面,携带液滴进入上升通道加速流动,烟气中烟尘被加湿粒化,二氧化硫被脱硫剂吸收。
随着负荷增加,烟气流速提高,流动阻力加大,液面低于低液位溢流管,液面与冲击管出口处空间增大,上升通道内烟气流速迅速提高、动压加大、静压减小,套管两侧形成压力差。套管外侧液体通过排孔流入上升通道与上升气流混合,烟气中的烟尘被加湿粒化,二氧化硫被脱硫剂吸收。当负荷继续升高时,烟气量增加,流动阻力增加,套管内液位下降,套管外液位上升,高液位溢流管限制了套管外的液位。随着负荷的进一步提高,套管内液位下降,当负荷稳定时套管两侧液位固定,此时套管内液位与冲击管出口处之间的空间较大,下降气流在此空间转向流动,速度滞流动压转化为静压,在排孔两侧形成压力差,烟气通过排孔进入液相形成鼓泡。总气量分为两部分:一部分由上升通道流出,另一部分通过排孔流出。流量比例与上升通道几何尺寸、烟气流速、携带液量、排孔开孔率以及孔排列方式有关,两部分流动阻力相等。
3 实验装置
以石灰浆液为脱硫剂的双液位喷射鼓泡烟气脱硫除尘实验装置结构见图3,模拟烟气垂直进入冲击管在出口处卷吸液体向上流动,此过程中烟气被加湿冷却,烟气中的二氧化硫和烟尘与脱硫剂接触被吸收和去除。经除尘和脱硫后的烟气转向向上流动,在撞击挡板作用下水雾被分离,净化后的烟气由引风机排出。脱硫剂循环泵将脱硫剂不断补入塔内以保证塔内液位,正常工作时脱硫剂通过高液位溢流管进行循环。调整二氧化硫瓶的阀门,可以改变二氧化硫浓度,通过测压管可以测得在不同烟气流量下的装置阻力。烟气分析仪可以测出烟气中二氧化硫浓度的瞬时值和积分值。实验规模:模拟烟气量200~1000m3/h,烟气进口处二氧化硫质量浓度700~850mg/m3,空塔流速1~3m/s。
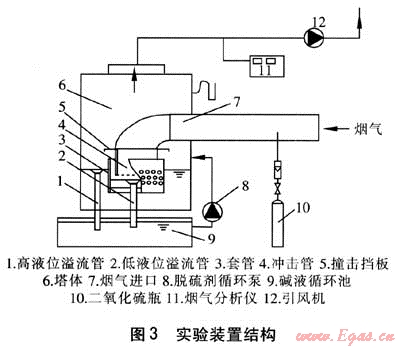
4 实验结果分析
脱硫剂pH值是影响脱硫效率的一个重要参数,也是脱硫过程中可调的参数。选择适当的pH值,不仅能够保证足够高的脱硫效率,还可以降低运行成本,保证脱硫系统的稳定运行。实验选择的石灰脱硫剂体积分数为10%;h为高液位溢流管管口距冲击管出口的距离,分别取50、100mm;低液位溢流管管口距冲击管出口的距离为20mm。脱硫剂pH值对脱硫效率的影响见图4。由图4可知,脱硫剂pH值为3.8~6.0时,脱硫效率随pH值的增加变化较快;pH值>6时,脱硫效率变化缓慢。h=100mm时,喷射速度提高,引射的液量增加,鼓泡通过液层的高度和运动的距离增加,气液交换的时间延长,脱硫效率较高,阻力随之增大。
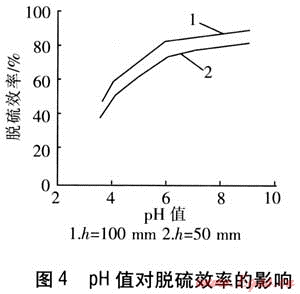
冲击管出口烟气流速对烟气压力降的影响见图5。由图5可知,当h=50mm、冲击管出口烟气流速为5.0~8.4m/s时,液位由低液位溢流管控制,气体通过冲击管出口与液位高度为20mm的空间发生气体卷吸液体的现象。随着流速的增大卷吸现象加剧,被卷吸的液体量增加,气液接触主要在上升通道内进行,气体压降随流速增加。当冲击管出口烟气流速超过8.4m/s时,液位开始下降,低液位溢流管失效,冲击管出口与液位形成的空间变大,上升通道内烟气流速迅速提高,动压加大、静压减小,套管两侧形成压力差,套管外侧液体通过排孔流入上升通道与上升气流混合。下降气流在此空间转向流动,速度滞流动压转化为静压,在排孔两侧形成压力差,烟气通过排孔进入液相形成鼓泡。当冲击管出口流速为18m/s时,烟气压力降为1300Pa。
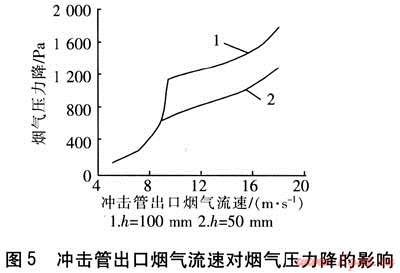
当h=100mm、冲击管出口烟气流速为5.0~9.0m/s时,液位由低液位溢流管控制。当冲击管烟气出口流速超过9.0m/s时,液位开始下降,低液位溢流管失效,随着冲击管烟气出口流速的进一步提高,烟气压力降随之增大。当冲击管出口烟气流速为18m/s时,压力降为1800Pa。总气量分为两部分:一部分由上升通道流出,另一部分通过排孔流出。流量比例与上升通道几何尺寸、烟气流速、携带液量、排孔开孔率以及孔排列方式有关,两部分流动阻力相等。
5 工业应用
某脱硫除尘系统的结构见图6。烟气进入均压箱后,向下进入喷射鼓泡管,含尘烟气进入冲击管,冲击液面,质量大的烟尘接触液面被捕集,烟气转向通过由冲击管和套管形成的通道向上流动。在通道内流速提高,静压减小,套管外部液体被引射通过套管的排孔流入通道内与上升气流激烈混合后被加速,烟气中的烟尘在与液体混合过程中被加湿、粒化,其中的二氧化硫在与脱硫剂混合过程中被中和吸收。液气混合物流出上升通道遇撞击挡板后,强化了气液接触,并使得液滴与气体分离,气流向上流动,液滴流回液面。除尘脱硫后的烟气转向向上流动进入上升管,在挡水板的作用下,大颗粒的雾滴被除下。净化后的烟气经除雾器除掉细小水滴后排出,脱硫后的脱硫剂通过排液口和高液位溢流管流回碱液循环箱,脱硫剂循环泵将脱硫剂通过脱硫剂循环管送入塔内循环使用。烟尘及脱硫生成物的沉渣沉入池底由刮渣机清除。
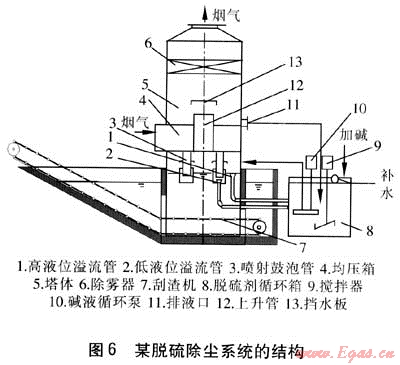
6 结论
① 双液位喷射鼓泡烟气脱硫除尘装置适用于集中供热锅炉的烟气脱硫除尘,当低负荷和封火状态时,低液位溢流管能保证低液位与冲击管出口处留有烟气通道。
② 城市集中供热锅炉房烟气脱硫改造时,采用该技术不需要另设沉降池,脱硫生成物和烟尘随炉渣一同排除,解决了城区老锅炉房面积紧张的问题。
③ 双液位喷射鼓泡烟气脱硫除尘装置能保持锅炉负荷变化在30%~100%时的除尘效率和脱硫效率稳定。根据测试结果,以石灰为脱硫剂,脱硫剂的pH值可控制在4~7,体积分数在10%左右。烟气压力降为1600Pa时,脱硫效率大于80%,除尘效率大于98%,设备不结垢,运行可靠,脱硫效率稳定。
参考文献:
[1] 陈向锋,刘晓彗.氧化镁在烟气脱硫中的应用[J].海湖盐与化工,2006,(3):34-36.
[2] 曹霞,陈秀萍.浅谈氢氧化镁法脱硫技术[J].有色冶金设计与研究,2000,(1):47-51.
[3] 崔可,柴明,徐康富,等.回收法氧化镁湿法烟气脱硫机理和工艺基础研究[J].环境科学,2006,(5):846-849.
[4] 雷士文,雷世晓,王德敏.氨法烟气脱硫脱硝的技术特征[J].电力环境保护,2006,(2):32-34.
[5] 张慧明,王娟.应用烟气脱硫技术控制燃煤工业锅炉SO2污染[J].电力环境保护,2006,(1):13-16.
[6] 吴忠标,刘越,谭天恩.双碱法烟气脱硫工艺的研究[J].环境科学学报,2001,(5):534-537.
[7] 金国根.CT-121湿式脱硫工艺的技术特点及调试[J].电力建设,2005,(8):48-52.
[8] 温冬,温高,于晓蕾.喷射鼓泡池阻力计算经验公式研究[J].科技创新导报,2008,(29):223-223.
[9] 翟云波,魏先勋,张德见.喷射鼓泡法烟气脱硫工艺[J].污染与防治技术,2002,(4):37-39.
[10] 孙世利,朱晓帆,苏仕军,等.用喷射鼓泡反应器进行烟气脱硫[J].化工环保,2005,(4):323-326.
[11] (以色列)TARNIR A(著),伍沅(译).撞击流反应器-原理和应用[M].北京:化学工业出版社,1996.
[12] ZHENG Y J,KIIL S,JOHNSSON J E. Experimental investigation of a pilot-scale jet bubbling reactor for wet flue gas desulphurization[J].Chemical Engineering Science,2003,(20):4695-4703.
(本文作者:彭铁成 天津理工大学动力系 天津 300383)
您可以选择一种方式赞助本站
支付宝转账赞助
微信转账赞助