国内外两种高含氮天然气液化工艺的对比分析
(本文作者:商丽娟 郭方飞 曲顺利 姚云 中海油山东化学工程有限责任公司)
摘要:为选择高效优化的高含氮天然气液化工艺,介绍了国内外两种典型的高含氮天然气液化工艺一国外常用的涡流管制冷器液化工艺和国内常用的膨胀机膨胀制冷液化工艺,通过模拟计算对其优缺点进行了分析对比。结果表明:涡流管制冷器液化工艺技术先进、工艺简单、操作弹性好,但是针对含氮量较高的天然气,其液化能耗较高、脱氮效果较差、甲烷回收率较低;膨胀机膨胀制冷液化工艺的优点是能耗相对低、脱氮效率高、甲烷回收率高,缺点是操作弹性较差。以某一含氮量较高的天然气作为原料,从液化单元功耗、脱氮率、甲烷回收率、投资成本等方面对两种液化工艺参数进行了比较,结论认为在针对高含氮量天然气进行液化时,膨胀机膨胀制冷液化工艺具有较大的优势。
关键词:天然气;液化;脱氮;甲烷回收率
天然气液化处理能够实现天然气的便捷运输,有效回收边缘天然气。天然气主要成分是烃类,但是国内外很多含油气盆地产出的天然气中含氮量较高。当天然气中含氮量较高时,不仅热值低、集输过程中能耗大,而且不能直接用作某些化工原料和汽车燃料。因此脱除其中的氮气,是提高天然气综合利用价值的重要途径。目前,普遍应用的脱除天然气中氮气的方法是深冷脱氮[1~3],国外主要采用俄罗斯涡流管制冷器液化工艺,国内主要采用膨胀机膨胀制冷工艺。
1 高含氮天然气的液化工艺
1.1 涡流管制冷器液化工艺
涡流管制冷器液化工艺主要采用了俄罗斯专利设备涡流管进行制冷[4],其流程如图1所示。进入液化单元的原料净化气先经过压缩机压缩到约20MPa,与经过压缩的循环气(20MPa)混合进入预冷换热器,利用预冷系统提供的冷量,将混合气预冷到约-20℃,再进入主换热器,利用循环气的冷量,将混合气的温度降至-80℃左右,其中一股通过涡流管制冷器降压后进入分离器1,另一股通过涡流管制冷器降压后进入分离器2。分离器1的气相分为两部分:一部分作为循环气回到主换热器与混合气交换热量,冷却混合气;另一股作为分离器2的热源输入(相当于再沸器),经冷却冷凝后进入分离器3,液相作为分离器2的冷源,气相则为含氮量较高的氮甲烷混合气,到换热器复热后排放作为他用(比如燃料)。分离器1的液相进入分离器2,进一步与涡流制冷器出口的混合物在分离器2中进行气液分离,液相作为液化天然气(LNG),送往LNG储罐,气相被卷吸进涡流管制冷器1。LNG储罐内蒸发气(BOG)被卷吸进涡流管制冷器2。该工艺过程简单,液化操作弹性好。
1.2 膨胀机膨胀制冷液化工艺
膨胀机膨胀制冷液化工艺通常是将制冷剂压缩后,经过膨胀机膨胀至低温,提供天然气预冷、冷凝、过冷的冷量,从而使天然气得以液化[5~12],其工艺流程如图2所示。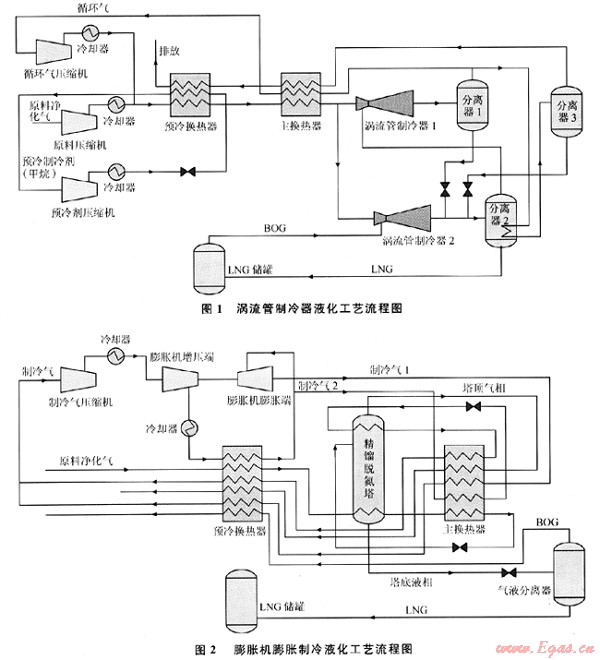
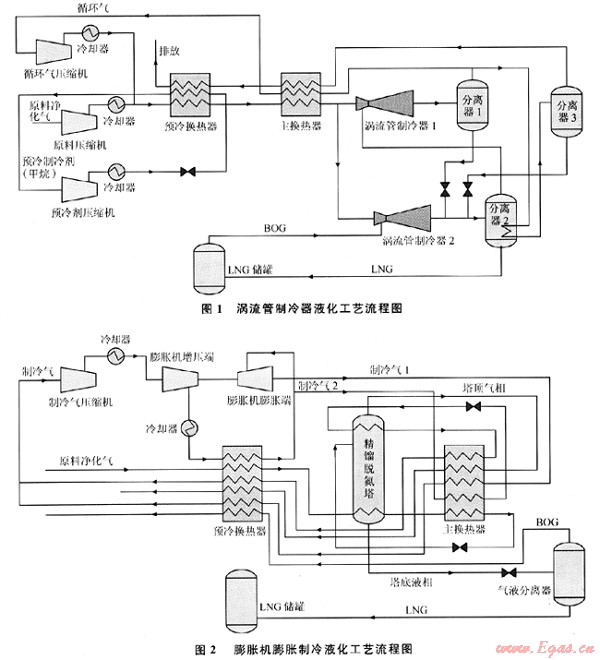
制冷剂经压缩机压缩到1.5MPa左右,再经膨胀机增压端继续增压、冷却器冷却后(40℃)进入冷箱,在冷箱中经过预冷,一部分制冷剂进入膨胀机膨胀做功,降温降压,进入主换热器作为主要的冷源,另一部分制冷剂在主换热器中过冷后经过节流降温,作为精馏脱氮塔上部冷却器的冷源,产生回流液。
原料净化天然气进入预冷换热器预冷,之后作为精馏脱氮塔塔底再沸器的热源进入精馏塔塔底换热,温度继续降低,从精馏塔再沸器出来后,进入主换热器换热至天然气全部液化,液化后的天然气经过节流后,进入精馏塔脱氮,脱氮后的饱和LNG从塔底流出,经过节流降温过冷,进入LNG储罐,生成的少量BOG去换热器复热作为燃料去其他单元。该工艺换热器中流股较多,板式换热器及冷箱制造较为复杂。
2 两种工艺的对比分析
2.1 脱氮标准
目前国内外LNG产品标准对氮气的含量都没有明确的规定。根据欧洲标准EN 1160-96,LNG产品中的氮含量(摩尔分数)应小于5%,而经验表明,只要控制LNG中氮含量小于1%,并加强蒸发气的监测,就可以避免LNG储运过程中的翻滚现象[13]。而参考多种LNG组成,发现I.NG中氮含量基本上小于1%,大于1%的较少。因此,本例中暂以摩尔分数小于1%作为脱氮评价标准。
2.2 计算条件
天然气液化规模设为每天生产相当于3×104m3气态气的LNG,即1250m3/h,储存压力为0.3MPa。
原料净化气的组成如表1所示。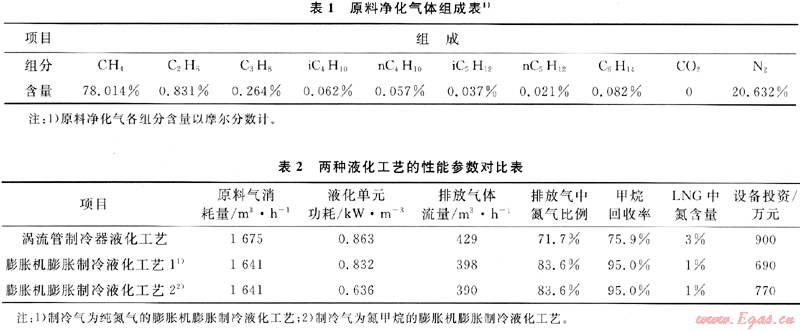
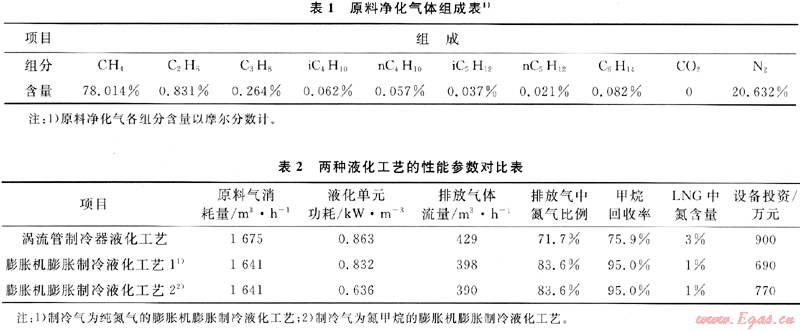
2.3 计算结果
利用Hysys过程系统模拟软件,对原料净化气的液化过程进行了模拟。采用两种不同的液化工艺,各项性能参数对比如表2所示。
对比可知:①涡流管制冷器液化工艺的原料气消耗量大于膨胀机膨胀制冷液化工艺,且有大部分冷气作为循环气,气量为5080m3/h,即初始开车时系统中要多出5080m3/h的原料净化气(折合12120m3/d)。②涡流管制冷器液化工艺液化单元功耗高于膨胀机膨胀制冷液化工艺(尤其是当膨胀机膨胀制冷液化工艺采用氮甲烷制冷气时,涡流管制冷器液化工艺液化单元功耗高出36%)。③涡流管制冷器液化工艺排放气体中的氮含量大于膨胀机膨胀制冷液化工艺,甲烷的回收率低,导致其LNG中氮气的含量较大,如果按照小于1%含氮量(摩尔分数)的标准执行,该工艺不能满足脱氮要求。④从整个液化单元(包括原料气压缩、遇冷系统、循环气压缩)的设备投资来看,涡流管制冷器液化工艺由于要将气体压缩到20MPa,所需设备防爆等级较高,设备投资也约高出膨胀机膨胀制冷液化工艺15%。⑤但是涡流管制冷器液化工艺操作灵活,进入原料气即可快速成液,生成LNG,这是其最大的优越性。
3 结束语
针对高含氮量的天然气液化,通过模拟计算,对涡流管制冷器液化工艺和膨胀机膨胀制冷液化工艺的主要工艺参数进行了对比分析,结果表明在原料气消耗量、液化单元功耗、LNG中氮气含量、设备投资等方面,膨胀机膨胀制冷液化工艺均优于涡流管制冷器液化工艺。
参考文献
[1] 刘成军,王志刚,钟建强.天然气脱氮工艺综述[J].石油规划设计,2000,11(4):18-20.
[2] 李怀印.海外油田液化气回收技术[J].石油与天然气化工,2010,39(3):200-203.
[3] 王天明,邵拥军,王春燕,等.中小型液化天然气装置净化和液化工艺研究[J].石油与天然气化工,2007,36(3):191-193.
[4] 黄志光,王荣顺,石玉美,等.小型天然气液化装置的研制现状与前景[J].低温工程,2002,130(6):59-62.
[5] 李素燕,马彩风,刘政委,等.小型氮膨胀天然气液化流程的设计及优化分析[J].低温工程,2009,16(2):47-51.
[6] 石玉美,顾安忠,汪荣顺,等.混合制冷剂循环液化天然气流程的优化分析[J].工程热物理学报,2000,21(4):409-412.
[7] 位雅莉.天然气液化工艺模拟与分析[D].成都:西南石油学院,2004.
[8] 蒲亮,李恩道,高长永,等.天然气液化流程的计算及热力学分析[C]∥第八届全国低温工程大会暨中国航天低温专业信息网2007年度学术交流会论文集.北京:中国制冷学会低温第一专业委员会,2007:112-116.
[9] 王健敏,皇甫立霞,郭开华.美、欧LNG标准NFPA59A和EN1473的比较分析[J].天然气工业,2010,30(1):114-115.
[10] 王保庆.天然气液化工艺技术比较分析[J].天然气工业,2010,30(1):111-113.
[11] 李士富,呼延念超,王继强.基本负荷型天然气液化HYSYS软件计算[J].石油与天然气化工,2009,38(5):371-374.
[12] 李士富,呼延念超,李亚萍.调峰型天然气液化HYSYS软件计算[J].石油与天然气化工,2010,39(1):1-2.
[13] 王遇冬.天然气处理原理与工艺[M].北京:中国石化出版社。2009:204-206.
(本文作者:商丽娟 郭方飞 曲顺利 姚云 中海油山东化学工程有限责任公司)
您可以选择一种方式赞助本站
支付宝转账赞助
微信转账赞助