摘要:沁水盆地南部煤层气田具有复杂山地地貌、低压生产和低成本开发等特点,在生产中存在数据获取、设备控制和安全保障等一系列问题。为此,①通过自主研发井场无线采集技术,在国内煤层气生产中率先实现了全井场生产数据的无线采集、传输,实现了橇装施工和快速链接,解决了山区复杂地貌生产数据采集及传输的布线难题,减少了现场维护工作量;②打破煤层气田生产与监控管理站点间的地域界限,应用基于ArchestrA Framework架构的网络化监控技术进行二次开发,通过模板化开发、网络化实施、多用户协作、集中化存储,实现了煤层气自动化系统“两级三地”的远程部署、分布式监控模式;③按照“缓慢、长期、持续、稳定”的抽排基本原则,建立起了煤层气智能排采控制模型,以排采过程中液面高度、液面下降速度、井底流压、套压等为主要控制参数,采用智能排采技术,实现了排采设备的生产参数自动调整,改变了煤层气井固定的生产制度,降低了对煤层的伤害。运用以上技术,建成了管理控制521口排采井、6座集气站和1座处理中心的自动化系统,达到了平稳运行、安全生产、降低劳动强度、提高生产管理水平、实现规模效益的目的。
关键词:沁水盆地南部;煤层气田开采;规模自动化;数据无线采集;网络化监控;智能排采
沁水盆地南部的煤层气田具有“低压、低产、低渗、低饱和”的特点,本文以满足煤层气气田“低成本、大规模开发”的需要[1],以沁水盆地南部煤层气田樊庄区块为例,重点介绍了一系列适用于山地地貌煤层气田开发的自动化技术得以规模化应用的情况。希望对国内煤层气田的开发建设有借鉴作用。
1 煤层气田开发方案概述
煤层气采、集、输的流程大致分为:煤层气井通过排水降压,解析采气,单井气采用串、并联方式进入集气站;经过集气站分离、增压后,再通过集气管线输往中央处理厂;通过分离、增压、脱水处理、计量后,经外输管线输入西气东输管道[2]。
自动化系统建设作为煤层气田开发的重要组成部分,采用软、硬件一体化的规模解决方案,主要根据生产现场相关工艺流程和控制参数要求,进行低成本、适应山地特点的煤层气排采井、集气站、中央处理厂生产参数数据采集、传输、排采调控;远程实时监控、管理等相关技术的研发和规模应用。下面就规模自动化技术进行介绍。
2 规模自动化技术系列
2.1 研发原则
1) 本着安全可靠、规模应用的思想,研究、推广符合煤层气田开发要求的自动化技术,形成先进、低成本适于规模开发的自动化技术系列。
2) 满足煤层气田生产安全和人身安全的要求,缓解人力资源紧缺的状况,配合地面工程取得规模效益,实现采、集、输系统生产平稳运行。
2.2 规模自动化技术
2.2.1煤层气田井场数据无线采集、远程测控技术
为解决排采井生产数据的采集、参数的远程调节和设备远程启停控制的问题,研发了井场无线采集、远程测控技术,采用微功耗无线传感器技术,在国内煤层气生产中率先实现了全井场生产数据的全天候无线采集、传输,各个监测点无电缆连接,解决了山区复杂地貌生产数据采集及传输的难题,实现了橇装化施工,减少了现场施工和维护工作量,突破了单井传统的数据采集方式。
该技术主要由无线数据采集控制器(RTU)和生产参数无线采集模块组成。
1) RTU是整个系统控制核心;安装在各个排采井上,可直接接入井底压力、电机启停状态等检测信号,可直接输出电机启停等控制信号。同时通过短距离无线通讯模块,实现载荷、压力、流量等参数的采集,并将多项参数融合传输至远端中控室。
2) 生产参数无线采集模块;引入网络传感器理念,研发了一系列具有微处理器的无线传输模块和无线网络传感器,使用高能电池供电。同井场传感器间由地址区分,采用统一频点,形成智能微型网络,实现RTU与传感器之间的无线通讯,不受井场环境的影响。各个井场之间则由不同频点区分,构成区域性监控群,取消了RTU与传感器之间的电缆连接线。
2.2.2基于ArchestrA Framework架构的网络化监控软件开发
随着网络技术的发展,网络架构软件以其分散的数据处理、良好的远程交互、可扩展的系统结构已经被越来越多的人认可。
为了满足相距从几千米到几十千米不等的不同地域煤层气田生产、管理站点的不同监控需求,基于ArchestrA Framework架构的网络组态解决方案,进行二次开发。组态软件系统由工程师站、数据服务器、浏览服务器、监控机等组成,采用星形网络连接,通过模板化开发、实施网络化、多用户协作、集中化存储,实现了煤层气自动化系统“两级三地”的远程部署、分布式监控模式。极大地节省了安装、调试和维护的人员和时间,提高了工作效率。
2.2.3煤层气井智能排采技术
煤层气井生产是一个较长时期的排水-降压-采气过程[3]。煤层气井的排采控制技术对煤层气高效生产有重要影响。合理的排采工作制度可以避免煤储层受到伤害,确保气井的高产、稳产,保证资源最大化的采出。不合理的排采方式,轻则影响排采效果,重则对气井产能造成难以恢复的伤害。国外煤层气定量排采与自动调控设备和软件的价格昂贵,单井约需要80万元,核心技术引进困难,且国外的技术也不完全适合国内复杂地质环境下的排采生产[4]。
按照“缓慢、长期、持续、稳定”的抽排管理基本原则[5],以井底流压、井口压力的实时监测为基础,建立了煤层气智能排采控制模型,排采过程中以井筒液柱高度、液面下降速度、井底流压、套压、产气量、产水量、粉煤灰等为主要控制参数;自主研发自动调控设备和软件,采用PWM脉宽调制技术,实现了排采设备按照设定值进行生产参数自动调整,改变了煤层气井固定的生产制度,降低了对煤层的伤害,以保证压降面积扩大与解吸速率的良好匹配,促进了单井产量实现高产、稳产。实现了平稳降压,达到“控制准确、稳定生产、长期开发”的目的。根据煤层气排采不同阶段的需要,智能调控的方式有2种:有序降压控制法和恒压控制法。智能排采系统原理见图1。
3 应用情况
3.1 煤层气田井场无线采集、远程测控技术应用情况
目前,华北油田公司在山西沁水盆地实施的煤层气SCADA系统系统,已覆盖了521口单井、6座集气站及1座中央处理厂,实现了单井全部监控和集气站、处理中心重点工艺流程、设备自动控制,重要设备全天视频监视。
3.2 网络架构监控软件应用情况
煤层气自动化监控系统由多人协作同时开发完成,组成由21台工控机组成的“两级三地”远程监控网络,分布在方圆100km2的山区,最远处距监控点70km,覆盖了整个煤层气由井、站、处理厂工艺流程全过程。图2为某个区域单井监控界面示意图。
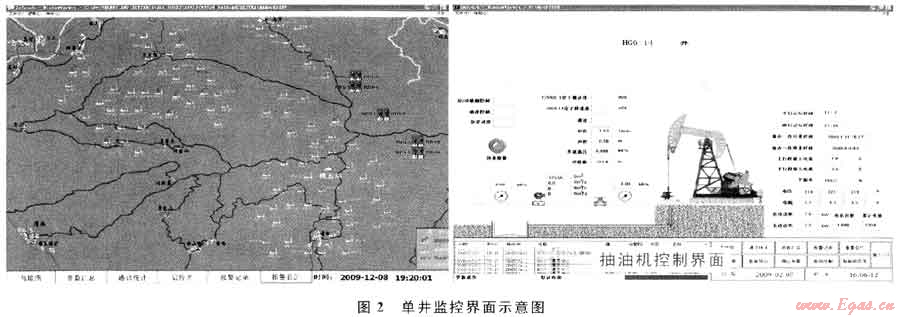
3.3 智能排采技术现场应用情况
实现了对不同种类排采设备的自动控制,实现了参数的采集(运行时间、管压、套压、井底流压、瞬时气量、变频器电流、变频器频率、泵扭矩、泵转速和沉没度)和远程自动液面控制功能,实现了排采井恒液面/变液面控制,达到了煤层气排采井的生产要求,为动态调整生产参数提供了新的方法,使排采井的高产、稳产成为可能。
4 结束语
山西沁水盆地南部数字化煤层气田示范工程通过3年多的自动化系统建设,在国内率先采用低成本可规模化推广的自动化技术,形成了动态监控、平稳控制、安全调度为特色的具有自主知识产权的数字化系列技术,实现了煤层气生产过程自动化管控,达到了全岗位无人值守,全过程Ih动控制,全方位监视管理,减少了用工,减轻了劳动强度,降低了操作成本,极大地提高了经济效益。同时,最大限度地满足了煤层气开发和安全生产要求,建成了“我国首个数字化、规模化煤层气田示范工程”[6]。为今后进一步开发煤层气能源,建设相关配套自动化系统奠定了技术基础。
1) 通过煤层气田井场数据无线采集、远程测控技术应用,建成了管控521口单井、6座集气站、359km采集气管线和1座年处理10×108m3的处理中心的自动化系统。实现了平稳运行、安全生产;减轻了劳动强度,降低了操作成本;提高了生产管理水平,年生产煤层气能力已达6×108m3,实现了新能源的规模化商业化运营,实现了规模效益。
2) 随着自动化技术的规模化应用,简化了数据处理和指令下达的流程,可以有效提高生产管理方面的感知能力和快速反应能力,使生产管理向扁平化、集约化模式改变,实现了“两级三地”管理模式。
3) 通过适应煤层气排采规律的智能排采技术应用,形成了一套完善的无人值守、智能煤层气井排采工艺技术,为自动化技术在煤层气开发领域的大规模应用开拓出新的方向。
参考文献
[1] 许茜,薛岗,周玉英,等.沁水盆地煤层气气田集气站标准化设计的经验与体会[J].石油工程建设,2010,36(1):104-105.
[2] 陈仕林.煤层气田地面集输工艺发展现状[G]∥中国煤炭学会煤层气专业委员会,中国石油学会石油地质专业委员会.2008年煤层气学术研讨会论文集,北京:地质出版社,2008:413-417.
[3] 张建国,苗耀,李梦溪,等.沁水盆地煤层气水平井产能影响因素分析——以樊庄区块水平井开发示范工程为例[J].中国石油勘探,2010,49(2):49-54.
[4] 丁闫,温欣,葛藤,等.煤层气井监控系统建设方案及其应用[J].煤田地质与勘探,2010,38(5):19-22.
[5] 张义,鲜保安,孙粉锦,等.煤层气低产井低产原因及增产改造技术[J].天然气工业,2010,30(6):55-59.
[6] 岳双才,宋学功.我国首个数字化煤层气田示范工程投产[N].中国石油报,2009-11-18(1).
(本文作者:赵立宁1 李鑫1 李洪涛1 杨超1 孟晓强1 赵达2 1.中国石油华北油田公司采油工艺研究院;2.北京中油瑞飞信息技术有限责任公司)
您可以选择一种方式赞助本站
支付宝转账赞助
微信转账赞助