摘要:作为一种特殊的炉型形式,天然气加热炉采用中间载热介质间接加热的方式,是天然气生产、输送和应用中的主要耗能设备。为了节能降耗、提高加热效率,必须结合工程实际的需要,优化加热炉的结构,设计制造出高效节能的天然气加热炉。为此,分析了天然气加热炉传热的薄弱环节及其强化措施,针对天然气加热炉大筒体内换热面的常规布置形式存在的缺陷,提出了旋转加热和冷却受热面以及在受热面之间加装导流板两种简单而有效的天然气加热炉改良结构,使中间载热介质形成整体有组织的顺畅流动并强化传热,从而达到节能降耗和提高天然气加热炉效率的目的。以上两项技术已获得国家专利授权。
关键词:天然气加热炉;流场组织;旋转;大简体;中间载热介质
天然气加热炉常用于井口、计量站、接转站等,将天然气加热至工艺所要求的温度,以便进行运输、分离和粗加工等(图1)。
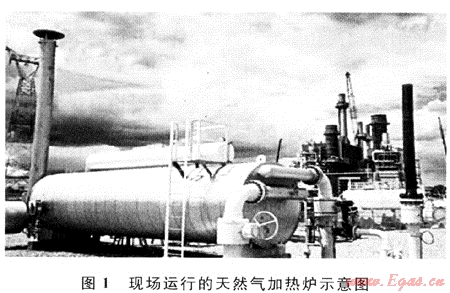
天然气在使用过程中也常需要加热,如在燃气发电机组中,其工艺对燃料气的压力、温度和露点要求很高[1],电厂使用的燃料气必须经过调压和加热处理。另外,在液化天然气(LNG)输配应用系统中,要使LNG气化,也必然会用到大量加热气化炉。
1 天然气加热炉的工作原理
天然气加热炉采用整体组装式结构,在卧式大容积筒体内布置火筒、烟管束等加热受热面和多回程对流管束等冷却受热面,筒内充注中间载热介质作为加热和冷却受热面之间的传热媒介,帮助冷、热两种流体达到传热的目的,中间载热介质可采用水、乙二醇溶液和导热油。通常,加热和冷却受热面沿大筒体圆截面中心轴呈轴对称布置,火筒和烟管束位于水平轴的下方,对称布置于垂直轴的左右侧;多回程对流管束位于水平轴的上方,各回程也对称布置于垂直轴的左右侧,如图2所示。
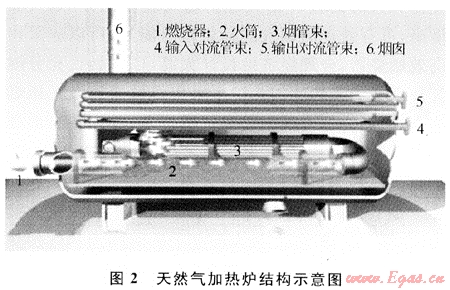
天然气加热炉工作时,用燃料燃烧产生的热量加热需要加热以达到工艺要求的工业用天然气。燃料和空气经燃烧器混合后喷入大简体下部一侧的火筒燃烧产生高温烟气,烟气经火筒折入大筒体下部另一侧的烟管束,最后经烟囱向上排入大气。在该过程中,高温烟气将热量通过火筒壁和烟管束壁传递给中间载热介质,中间载热介质吸热升温;同时中间载热介质将大部分热量通过对流管束壁面传递给需要加热的工业用天然气,中间载热介质放热降温。
天然气加热炉是采用中间载热介质间接加热的一种特殊的炉型形式,工作运行可靠,但启动慢,是天然气工业中的重要耗能设备之一。提高天然气加热炉的热效率,显然是一个必须解决的问题。
2 天然气加热炉传热系统分析
对天然气加热炉来说,烟气、中间载热介质、需加热的天然气这三者是通过火筒、烟管束和对流管束进行换热的。火筒、烟管束和对流管束的材料均为钢材,其导热系数为定值,只有通过提高三者之间的传热系数,加热炉的热效率才能得到提高。研究人员对提高天然气加热炉热效率投入了大量的精力,主要考虑了烟气-中间载热介质、中间载热介质-被加热介质传热系统的换热情况。
2.1 烟气-中间载热介质传热系统
传统天然气加热炉的烟气-中间载热介质传热系统中,火筒和烟管热负荷的比例约为6:4,火筒负荷率偏大,导致火筒结构不合理,是造成天然气加热炉结构庞大、金属耗量高的一个重要原因。
火筒主要传递辐射热,且换热量份额大,因此燃烧器和火筒的设计是关键。燃气燃烧充分,烟气温度高,可有效提高烟气的辐射传热能力,所以应采用高效燃烧器,合理经济地设计火筒,以供燃气充分燃烧。现在的天然气加热炉多采用机械通风微正压燃烧方式,燃烧器为强制供风式燃烧器,并配备自动程序点火和熄火保护装置。较之自然通风燃烧方式,加热炉热效率更高、结构更紧凑。
烟管主要传递对流热,尽管其换热面积比火筒大,但换热份额少,在很大程度上影响到天然气加热炉的热效率、钢耗量和外形尺寸,因此需采取办法强化烟管的对流换热效果。缩小管径、提高烟气流速能够达到强化传热的目的,但烟气在高速流动下产生的阻力很大,必须提高强制通风能力,使成本上升。近年来,中国石油大学开展了采用三维内肋管作为加热炉烟管的研究,结果表明,烟气与三维内肋管的对流换热系数能达到光管的4.6倍[2],可以有效地提高天然气加热炉的热效率,降低金属耗量,但需要合理地控制烟气阻力。目前,三维内肋管的热力、阻力计算还依赖于实验资料。
为增强烟气和中间载热介质之间的换热,开展了将热管元件应用于加热炉的试验研究(通常是在烟管内插装热管元件)。由于烟管中的烟气温度比火筒低,采用相对便宜的碳钢一水低温热管就能满足要求。实践证明,热管元件对加热炉能起到良好的强化换热作用。经测试,热管加热炉的实际运行热效率为87%~88%,过量空气系数为1.04~1.17,排烟温度为160℃[3]。但热管的应用推广受到冷、热流道间的密封及热补偿等问题的制约。
2.2 中间载热介质-被加热介质传热系统
天然气加热炉的被加热介质是带压天然气,传统的气盘管一般做成蛇形盘管形式,它的优点是制作简单,易于布置在天然气加热炉内。为了提高传热效率,采取缩小管径、提高被加热介质流速的方法达到强化传热的目的,在设计时将蛇形加热盘管由大直径管改为小直径管组成的多回程管束,以取代传统大直径管盘。
为了强化中间载热介质与被加热介质的换热,也可采用真空相变技术。在密闭加热炉筒体内,将火筒与烟管束置于相变介质的液相空间内,对流管束置于相变介质的气相空间内。工作时,火筒与烟管束加热相变介质使其沸腾,载热介质与火筒和烟管束间产生沸腾换热。同时,产生的蒸汽上升,在对流管束的冷却下凝结,载热介质与对流管束间产生凝结换热。随后,液滴落下来重新汇入液相,如此反复循环。由于凝结换热和沸腾换热是高强度的对流换热形式,因此,与自然对流换热过程相比,相变换热过程具有更高的换热强度。实践证明,对一台1740kW加热炉进行真空相变换热技术改造后,运行效率将达到89.03%,节能效果显著[4]。但是相变传热受到饱和压力、对流管束排数尤其是不凝结气体的影响很大,更重要的是,由于真空加热炉主要是通过调节真空度来调节气相空间的温度,温度可调范围比常压天然气加热炉窄,操作弹性小,限制了其使用。
还可采用高效传热元件来优化对流管束结构。例如采用可拆卸式螺旋槽u型管束,换热系数一般可以提高50%左右[5],但采用螺旋槽管使对流管束阻力约增大一倍,另外,由于螺旋槽管的造价较高,一般根据被加热介质的性质与状态,经过综合评价后决定是否采用。
天然气加热炉的研究随着其应用的不断增加而深入,取得了很大的进展,但仍侧重于从增加气相侧的换热技术方面着手[6],忽视了对大简体内中间载热介质的流动与换热研究。
3 大简体中间载热介质流场的组织
在常压天然气加热炉的整个传热过程中,中间载热介质与火筒、烟管束和对流管束的传热形式为自然对流换热。贴近火筒和烟管束壁面的介质温度较高,形成上升流,对流管束附近的介质温度相对较低,形成下降流。通过测试简体内中间载热介质的温度分布发现,天然气加热炉大简体内换热面的常规布置形式存在如下缺陷[7](图3):①大简体内流场组织紊乱,这是因为上升流和下降流均是自发产生的,没有恰当的流道组织,二股流之间易发生对冲,造成流动不畅及加热不匀;②大筒体内流场上下温差较小,自然对流的动力小,加热受热面和冷却受热面之间的对流传热非常弱,传热效率低;③在整个流场中,还存在着不少流动死角,如大简体底部等。
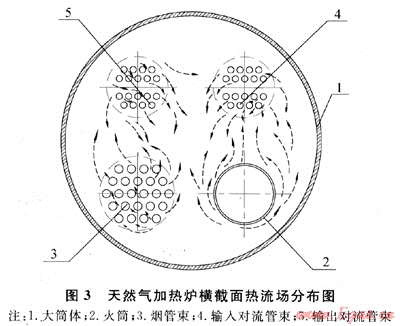
所有这些因素都不利于有效传热流场的形成,使加热和冷却受热面的有效利用降低,造成筒体内传热流场组织紊乱,从而使天然气加热炉效率低、能耗高。显然,中间载热介质传热过程的形成,亦即大容积简体内流场的组织是提高天然气加热炉效率的关键点之一。
3.1 天然气加热炉大圆筒旋转流场研究
针对天然气加热炉大筒体内无法形成有效传热流场的缺点,首先提出一种旋转型圆筒式天然气加热炉(国家实用新型专利:ZL200820057571.9):将大筒体内对称布置的加热受热面(即火筒和烟管束,以及冷却受热面)旋转适当的角度,使加热受热面尽可能置于较低的位置[8](如图4所示),这时大筒体内温度最高的火筒位于筒体的最下部,形成一股较强向上的热压,增大引起自然对流的动力,由于火筒、烟管束和对流管束内的流体存在温差,促使大简体内中间载热介质形成顺时针循环顺畅的热流场,消除大筒体底部的“死角”,达到强化传热,提高效率的目的。研究表明:该旋转角度以20°为最佳[9],旋转太小,达不到增大动力的目的;旋转太大,会导致烟管束与输入对流管束处于同一水平位置,反而破坏了顺畅流场的形成。

3.2 天然气加热炉筒内加装导流板组织流场研究
为加强天然气加热炉大筒体内有效传热流场的组织,提出一种大筒体内加装导流板组织热流场的改良结构(国家发明专利:ZL200810036446.4):在筒体上部的冷却受热面和筒体下部的加热受热面之间,沿简体轴向设置导流板,导流板的长度可按实际需要沿筒体轴向分割成几块,这样便于加工安装和提高使用效果,如图5所示。
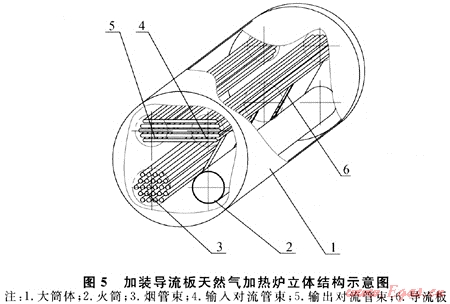
导流板的设置,合理分隔加热炉加热和冷却受热面之间的流动区域,中间载热介质在吸收筒体下方火筒和烟管束内的热量后,沿着导流板的方向形成均匀顺畅有组织的向上流动,然后将热量传递给上方的对流管束,加热低温天然气。中间载热介质放热后,沿导流板另一侧向下流动,形成循环均匀的流场。在火筒和对流管束之间加装弧形导流板,导流板挡住了火筒与输入对流管束之间的通道,使火筒周围的载热介质向烟管束上方流动,与烟管束周围的载热介质一起向上依次流经对流管束各流程放热后,向下回流到火筒周围,在大筒体内形成了整体大循环流场(图6)。弧形导流板与热流场的流线更贴切,能使大筒体内的流场更顺畅均匀,传热效果更好。
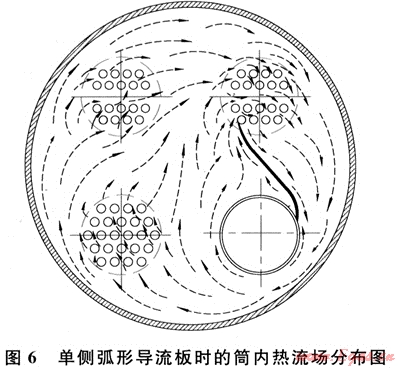
实际应用中,亦可布置双侧导流板(图7),火筒和烟管束周围的上升流在双导流板的引导下,分别流经各自上方的对流管束放热后,向下回流到火筒和烟管束附近,从而在大筒体内形成了更有效的双循环流场。
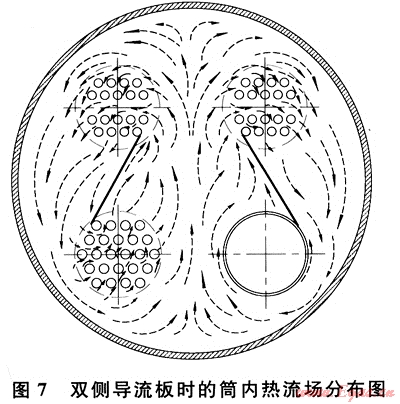
对于黏性较大的中间载热介质,如乙二醇,尤其需要这种导流型的强化传热方式。通过加装导流板,促使靠近壁面的热边界层变薄,引导中间载热介质在大筒体中形成整体有组织的顺畅流动,消除热流场死角,提高传热效率。就天然气加热炉的特殊传热结构和载热介质特性而言,在大筒体内加装导流板是一种有效的强化传热手段,效率可提高3%[10]。
4 结论
1) 天然气加热炉在研究应用微正压燃烧技术、螺旋管槽对流管束、三维内肋烟管强化传热技术、热管传热技术、相变传热技术等方面取得了较大进步。
2) 旋转加热和冷却受热面的布置结构优化了加热炉的整体传热效果,而无需额外投资。研究表明最佳旋转角度为20°。这种旋转型圆筒式天然气加热炉值得推广应用。
3) 在受热面之间设置导流板能优化天然气加热炉的整体传热结构,使大筒体内形成有效顺畅的流场,是一种简单而有效的改良结构,尤其对于乙二醇这种黏性大的中间载热介质,能够促进对流换热,提高传热效率,降低能耗。导流板的位置和形状等结构参数可根据使用条件和工艺要求进行优选。
参考文献
[1] 袁斌,羊东明,王颖,等.燃气发电机组的供气工艺[J].油气田地面工程,2001,20(2):30-32.
[2] 李清方.三维内肋管在水套炉上的应用[J].石油规划设计,2004,15(6):38-40.
[3] 张连明,王海,陈普信,等.热管式常压水套加热炉研究与应用[J].油气田地面工程,2003,22(12):24-25.
[4] 牛春庆,别如山,朱利民.相变换热技术在水套加热炉节能改造上的应用[J].节能技术,2003,21(5):32-33.
[5] 李清方,张国忠,张建,等.新型高效水套炉的开发研究[J].石油规划设计,2006,17(5):42-45.
[6] GARY H PALMER,PAULA WENDLAND,张华岩.油气田水套加热炉[J].天然气工业,2002,22(1):80-84.
[7] 郭韵,曹伟武,严平,等.天然气加热炉的可视化实验研究[J].上海理工大学学报,2009,31(4):327-331.
[8] 郭韵,曹伟武,严平,等.天然气加热炉结构与传热特性研究[J].上海理工大学学报,2009,31(3):251-254.
[9] 曹伟武,严平,郭韵,等.一种旋转型圆筒式气体加热炉:中国,ZL200820057571.9[P].2009-03-04.
[10] 曹伟武,严平,郭韵,等.一种圆筒式气体加热炉热流场的改良结构:中国,ZL200810036446.4[P].2008-09-10.
(本文作者:郭韵1,2 曹伟武2 严平2 钱尚源2 1.上海理工大学能源与动力工程学院;2.上海工程技术大学机械工程学院)
您可以选择一种方式赞助本站
支付宝转账赞助
微信转账赞助