摘要:作为常规地面管架或栈桥管廊方案的替代,LNG接收站卸料管道专用隧道是一种全新的技术解决方案,具有许多独特之处,为此,介绍了目前世界上仅有的两条卸料管道专用隧道——美国Dominion Cove Point LNG接收站和日本东京瓦斯Ohgishima LNG接收站卸料管道专用隧道的情况,并以广东省某地处于前期可行性研究阶段的LNG项目为例,分析了国内第一条LNG卸料管道专用隧道工程的内部系统相关设计和研究情况,提出了该类型隧道内系统设计应着重考虑的设计特点:横断面的基本形状;高等级安全性的保障;合适的操作和维护设施;连续监控系统的设置。该研究成果对更为广泛的低温管道专用隧道内部系统的设计和研究具有借鉴和参考意义。
关键词:LNG接收站;低温管道;专用隧道;设计
近年来,在国内液化天然气(LNG)接收站的研究与建设过程中,不断遇到新的技术课题和挑战,其中之一,就是LNG接收站卸料管道专用隧道的特殊设计问题。作为常规的地面管架或栈桥管廊的替代方案,LNG接收站卸料管道专用隧道内部设置有多种类型的工艺管道和公用系统管道。其受限空间的特点、LNG的低温特性、距离LNG接收站区较近及对高度安全性的要求,使得这种隧道内部各种系统的设计既不同于栈桥管廊和LNG接收站站区的相关设计,也不同于通常的天然气长输管道隧道内的设计。
为此,主要从使用安全和使用功能角度探讨该专用隧道的基本横断面设计、内部管道布置、相关维护、安全保障方案及监控设施等特殊问题。
1 国外LNG接收站卸料管道专用隧道介绍
根据公开文献和资料,在全世界诸多运行和在建的LNG接收站中,国外LNG接收站卸料管道专用隧道仅有2条,这2条隧道的共同特点是卸料管道与隧道部分地通过海底并通过立管与卸船码头相连接,隧道采取充氮密封保护方案,设置独立隔离的巡检通道。
1.1 Dominion Cove Point LNG接收站卸料管道专用隧道
Dominion Cove Point LNG接收站位于美国马里兰州切萨皮克湾,1974年建成,1978年正式运营后两年关停,于2003年7月重新运营[1],并于2008年开始新增两个16×104m3储罐的建设。
该接收站位于一个自然保护区,考虑到环境保护部门的要求和视觉上的协调,连接码头与接收站储罐区的LNG卸料管道放弃了传统的栈桥方案,而采取了专用隧道的方案[2~3]。卸船码头包括2个卸船平台,可以同时卸载2艘LNG运输船。卸船码头距离接收站2414m,全程采用1951m长的水下隧道(海岸线以外)和地下隧道(陆地部分)相连接。详见图1。
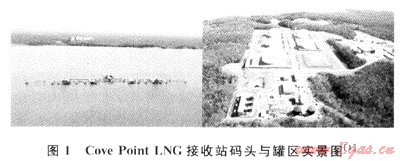
LNG卸料管道隧道内分为3个隔离区间,两侧空间分别布置一根32″(812.8mm)的LNG管道和一根14″(355.6mm)的蒸发天然气(BOG)返回管道,中间区布置公用系统管道、通讯仪表电缆及电力电缆,同时还用作人员巡检通道。两侧的低温管道空间采用充氮密封的方案[2~4]。陆地部分的地下隧道净宽8.36m,高5.33m,全长336m。这部分隧道是采用加强混凝土箱函形式的,盖板及四周均设置了防水层。水下隧道(海岸线以外)是由20个连续组装、配重、螺栓连接、混凝土外浇灌的钢板骨架内衬构成的,全长1615m,净宽8.36m,高4.88m[4]。
1.2 日本东京瓦斯Ohgishima LNG接收站卸料管道专用隧道
Ohgishima LNG接收站位于横滨湾。为了整体美观和突出海景的需要,采用了2000m长的盾构隧道连接接收站罐区和海上码头(离岸500m)的方案[5]。其示意图见图2。
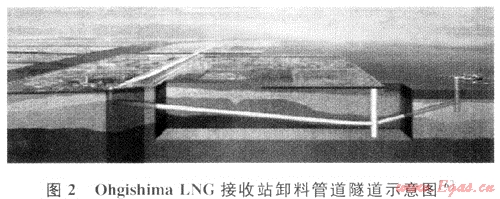
该低温管道隧道外径8.9m,内径7.2m,隧道顶部覆土最深达到60m。隧道横断面采用环形构造,内部分为2个相互独立的间隔区,一个是管道区,另一个是人员巡检通道。管道区内布置有40″(1016mm)的LNG卸料管道、20″(508mm)的BOG回气管道、8″(203.2mm)的保冷循环管道以及20″(508mm)的LPG接收管道、10″(245mm)的LPG回气管道、6″(152.4mm)的LPG循环管道,此外还有LNG/LPG排气管道、仪表风管道、氮气管道和水管道。巡检通道内布置有各类电缆和可燃性气体浓度、氧气含量测试仪器。管道区采用充氮保护方案[6]。出于空间利用的需要,隧道内管道区分为3层,最上面一层为LPG管道层,最下面一层为20″(508mm)和8″(203.4mm)的LNG/BOG管道、LNG/LPG排气管道及公用系统管道,中间层为最大口径的LNG卸料管道。在隧道顶部和中间层底部安装有3条测温光缆,供隧道内温度检测和低温液体泄漏检测使用。在隧道最下面一层底部安装了8条M1伴热电缆。
由于该隧道整体长度较长,在隧道中间设置了一个轴式竖井,既方便隧道内部施工期间的强制通风换气和焊接操作排气,也可作为运营期间发生事故情况下的排气通道使用。
上述2条国外LNG卸料管道专用隧道均已长期运行多年,安全记录良好。
2 国内LNG接收站卸料管道专用隧道设计
在国内广东省某地处于前期可行性研究阶段的LNG项目遇到同样的设计问题,这将是国内首条、世界第三条LNG管道专用隧道。该LNG站址距离海岸线较远,由于该地区生态旅游的环境保护要求,LNG卸料管道无法考虑地面管架或栈桥管廊方案,而是采用隧道方案穿越码头栈桥与接收站罐区之间的山头。卸料管道全长约2005m,其中栈桥部分325m,隧道部分580m,其余部分1100m,隧道出口距离储罐区450m。
在该项目LNG低温管道隧道研究和设计中,对以下4个主要方面进行了较为深入的研究。
2.1 U形膨胀弯(即靠型/门型补偿器)的尺寸、数量与隧道横断面尺寸
隧道横断面尺寸与LNG卸料管道U形膨胀弯的尺寸、数量的关系如下:膨胀弯的垂臂长度越小,则隧道内LNG管道的膨胀弯数量越多,隧道横断面尺寸较小,低温管道的费用则越高,隧道工程的造价越低;反之则相反。综合比选结果参见图3。
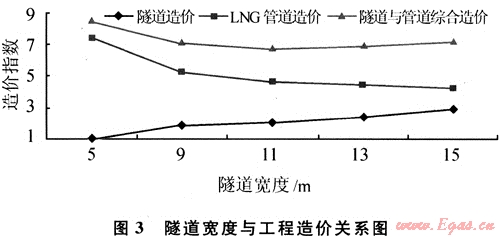
如果采用温差不变形的合金材料管道(36%镍钢管,此时膨胀弯的数量为0)时,隧道宽度为5m。此时管道本身的采办和安装造价非常高(据了解国外生产厂商仅有一家,就580m的较短长度和u形弯数量而言,综合造价过高),而且该36%镍钢管的焊接非常困难。经综合研究后,隧道内设置的膨胀弯垂臂宽度为8m,膨胀弯间距为88m,隧道内轮廓拟采用马蹄形断面形式,隧道内净尺寸为11m×8m。
2.2 隧道内采用充氮保护还是强制通风的方案选择
隧道内充氮和强制通风是可选择的两个基本安全保障方案,国外的两个工程实例均是采用管道区充氮的方案。充氮保护是为了万一发生少量LNG或天然气泄漏时,因隧道内几乎不存在氧气而阻绝燃烧或爆炸的发生。在这种条件下,隧道内层施工应达到尽可能高的气密性和水密性。而考虑到进入充氮环境下操作和维护的困难性,为了减少防腐刷漆维护的必要性和次数,隧道内的其他管道和管廊架均应采用不锈钢材料。可以看出,该方案对隧道自身的施工要求很高,发生泄漏情况下的维抢修工作难度也很大。
而强制通风方案本质上是稀释泄漏的天然气浓度以低于其燃爆下限,在工程实现和运行操作方面较为简单,对隧道施工的气密性要求一般,便于隧道内的巡检和维修工作,而且附带有热量交换功能。结合现有隧道施工技术能力、维护便利程度及事故反应时间等条件,通过综合比选和专家论证,本项目因地制宜地采用了强制通风的隧道方案,即平时用隧道顶部的射流风扇小流量通风、紧急情况下用栈桥侧隧道入口处的大排量鼓风机强制通风相结合的方案。
2.3 隧道内空间的布置
隧道内包括管道区域和人员通道两大区域。其中工艺管线包括46″(1168.4mm)的LNG卸料管道、28″(711.2 mm)的BOG回气管道、12″(304.8mm)的保冷循环管道和4″(101.6mm)的排气(VENT)管道,公用系统管道包括16″(406.4mm)的消防海水管道及其他小口径的氮气、仪表风、水管道及仪表电缆、电力电缆(参见图4)。低温管道均采用焊接连接,不设任何阀门或法兰。此外,作为防冷冻保障方案,在LNG卸料管道底部的管架上,设置M1电缆进行电伴热,用于隧道通风换热不足情况下的安全保障,其设计能力为18.0W/m。
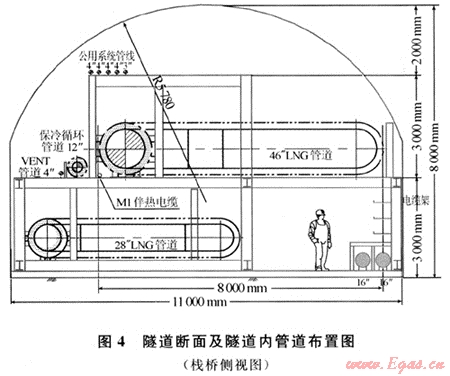
在充氮方案下必须设置独立的人员检修通道与逃生通道,但是,如果考虑采用常规通风与紧急强制通风相结合的保护方案,经过有关评估,可以取消单独隔离的逃生通道设置。
2.4 监控与报警设施
为确保对隧道内的安全状况进行实时监控和及时报警,隧道内还安装有FGS火气探测系统(FGS)、闭路电视系统(CCTV)、公共警报广播系统(PAGA)。FGS系统包括感温探测器、低温液体泄漏探测器、火焰探测器、可燃气体探测器、感烟探测器和含氧度测试仪等。此外,在隧道进出口设置门禁管理系统,确保进入隧道前得到正式的许可和进入期间得到实时安全监控。
3 LNG接收站卸料管道专用隧道的设计特点
LNG接收站卸料管道专用隧道内部系统在实现基本功能和高等级的安全性要求时,应着重考虑其下述几个基本特征:相对密闭(受限空间)、易燃易爆介质、低温特性和位置距离接收站罐区较近等。隧道内部系统设计应因地制宜,如本例LNG项目的卸料管道隧道采取了强制通风的方案,不再要求设置隔离的独立人行通道空间,而国外的两条隧道受条件限制采用强制通风方案是不合适的。一般来说,低温管道隧道设计需要考虑下述4个特殊问题,也即相应此类低温管道隧道内部系统的设计特点:
3.1 横断面的基本形状
影响隧道横断面形状的首要因素是隧道内管道的布置要求,包括LNG卸料管道、BOG回气管道、放空(VENT)管道、相关公用管道和电(光)缆等。起决定性作用的是最大口径的LNG管道U形膨胀弯的数量和膨胀弯的宽度,该两项参数应与隧道横断面进行共同优化,以满足综合工程造价最低的要求。其他影响因素还包括监控设施的安装空间、巡逻通道的设置要求等。
3.2 高等级安全性的保障
在受限(密闭)空间里布置有各种LNG/天然气管道有可能形成易燃易爆气体的混合物,而出于操作和维护的需要,应格外强调人员的安全性。因此,安全性设计应在杜绝LNG管道发生泄漏、尽快地检测到微量LNG/天然气的泄漏及防止隧道内积聚形成可燃气体混合物3个层面进行考虑。其基本措施应因地制宜地在隧道内充氮密封和强制通风2种方案中进行选择。另外,应着重研究是否需要单独设置隔离的人员通道。
3.3 合适的操作和维护设施
考虑到隧道及隧道内管线应满足LNG接收站设计寿命的需要,隧道横断面的设计应满足巡检、维修等维护性工作的要求,而且应尽可能采用免维护的材料和结构。由于隧道内低温管道与周围环境持续换热可能会导致出现结冰等问题,尤其当LNG或天然气管道的保温层温度低至0℃时会因管道的收缩而发生损坏,而且隧道地表面形成冷冻层后可能会对隧道自身的结构性能造成破坏,因此应采取措施尽可能地降低隧道内的湿度,并考虑安装加热设施。
3.4 连续监控系统的设置
为了确保隧道内各种设施能安全、稳定地运行,应对隧道内部各种设施进行持续的监控。
4 结论
通过介绍国外LNG卸料管道专用隧道的设计和运行情况,较为详细地分析和探讨了国内首条LNG卸料管道专用隧道内部系统研究和设计的情况,总结了该类型隧道内系统设计应考虑的特点,为国内其他LNG管道专用隧道的设计与实施提供了参照和范例,也为国内其他类型的低温管道专用隧道的研究提供了有益的借鉴作用。
参考文献
[1] LT.CMDR.MARK HAMMOND. Cove Point risk assessment[J].Proceedings,2005,62(3):87-91.
[2] STILES R E. Imported LNG to serve East Coast utilities[J].Pipeline Industry,1974,40(1):48-50.
[3] PERAINO J.CHASE B L,PLODOWSKI T,et al. LNG:From Ship to Shore[C].Houston:OTC,1976,1119-1127.
[4] P&GJ STAFF.6000-ft tunnel,LNG unloading facility Unique aspects of Cove Point terminal[J].Pipeline and Gas Journal,1975,202(7):60,62,66.
[5] NISHIKl0RI MINORU,MORI YOICHI,KASAHARA SHINICHI. The startup of the latest LNG base. Oogishima factory in Tokyo Gas[J].Piping Engineering,1999,41(7):15-22.
[6] ISAYAMA TERUHIRO,KATO TOSHIHIRO. Construction report for LNG receiving terminal of Tokyo Gas Ohgishima[J].NKK Technical Report,1999,167:56-61.
(本文作者:付子航 中海石油气电集团有限责任公司技术研发中心)
您可以选择一种方式赞助本站
支付宝转账赞助
微信转账赞助